Advanced Systems for Contamination-Free Cleanrooms: Ensuring Effective Cleanroom Environmental Control
Cleanrooms are meticulously controlled environments where even the smallest airborne particle or microbial presence can compromise product quality and safety. In industries like pharmaceuticals, biotechnology, electronics, and medical device manufacturing, maintaining a strict level of cleanliness and air purity is essential. Cleanroom environmental control systems—covering air filtration, temperature, humidity, and pressure—are the backbone of contamination prevention. Implementing advanced systems for environmental control not only maintains the required cleanliness levels but also enhances operational efficiency and regulatory compliance.
This article explores the advanced systems used in cleanrooms to achieve contamination control, the key elements of environmental monitoring, and the best practices for maintaining a contamination-free environment.
Why Cleanroom Environmental Control Matters
In cleanroom manufacturing, maintaining environmental control is vital for producing contamination-free, high-quality products. Environmental control encompasses the regulation of particles, microorganisms, temperature, humidity, and airflow within a cleanroom. Effective cleanroom environmental control is necessary for:
- Product Integrity: Ensuring that products are manufactured in contaminant-free conditions preserves quality, efficacy, and safety.
- Regulatory Compliance: Cleanrooms must meet stringent standards, such as ISO 14644 and GMP, which mandate strict environmental control and monitoring.
- Operational Efficiency: By minimizing contamination risks, environmental control systems reduce rework, recalls, and production delays, enhancing operational efficiency.
Key Elements of Cleanroom Environmental Control Systems
To maintain a contamination-free cleanroom, advanced environmental control systems monitor and regulate multiple variables. Here are the critical elements of an effective cleanroom environmental control system:
1. Air Filtration and Purification
Contaminant-free air is the foundation of cleanroom environmental control. High-efficiency air filtration systems remove particles and microorganisms, creating a stable, controlled environment.
- HEPA and ULPA Filters: High-Efficiency Particulate Air (HEPA) filters capture 99.97% of particles as small as 0.3 microns, while Ultra-Low Penetration Air (ULPA) filters trap particles down to 0.12 microns. HEPA filters are widely used in ISO Class 5-8 cleanrooms, while ULPA filters are ideal for ultra-clean environments, such as semiconductor manufacturing.
- Laminar and Turbulent Airflow Systems: Cleanrooms use laminar (unidirectional) or turbulent (non-unidirectional) airflow systems to direct filtered air through the cleanroom. Laminar airflow systems are ideal for critical areas, as they create a continuous air stream that removes contaminants. Turbulent airflow systems provide consistent air distribution across lower-class cleanrooms.
- Regular Filter Maintenance: Filters should be inspected and replaced according to usage and manufacturer guidelines. Routine testing and maintenance ensure that filters perform optimally, keeping air purity levels within the required standards.
2. Temperature and Humidity Control
Maintaining consistent temperature and humidity levels is essential in cleanrooms, as fluctuations can promote microbial growth or alter product properties.
- HVAC Systems with Precise Controls: Advanced Heating, Ventilation, and Air Conditioning (HVAC) systems regulate cleanroom temperature and humidity to maintain the stability of sensitive products. Precision control systems adjust environmental conditions based on cleanroom requirements.
- Dehumidifiers and Humidifiers: These systems add or remove moisture from the air, ensuring that humidity levels remain within target ranges to prevent condensation and microbial growth.
- Monitoring and Alarms: Real-time monitoring systems track temperature and humidity levels, issuing alerts when readings deviate from acceptable ranges. These systems help maintain compliance and mitigate contamination risks promptly.
3. Pressure Differential Systems
Pressure differential control prevents contaminants from moving between cleanroom zones, especially when multiple cleanliness levels are present.
- Positive and Negative Pressure Control: Cleanrooms often use positive pressure to prevent contaminants from entering critical areas. In contrast, negative pressure is used in containment areas handling hazardous substances, keeping contaminants within designated spaces.
- Pressure Monitoring Sensors: Differential pressure sensors monitor the pressure levels between adjacent cleanroom zones. Consistent monitoring and control ensure that air flows correctly, preventing cross-contamination.
- Sealed Entrances: Doors between cleanroom zones are designed to maintain pressure differentials. Interlocking doors prevent simultaneous openings, ensuring that pressure levels remain stable and contaminants are contained.
4. Environmental Monitoring Systems
Continuous monitoring is essential for verifying that cleanroom environmental conditions meet regulatory standards. Environmental monitoring systems provide real-time data, enabling cleanroom managers to maintain contamination-free conditions.
- Particle Counters: Particle counters measure airborne particle concentrations to ensure compliance with ISO standards. These devices monitor particle sizes and counts, ensuring that cleanrooms meet the required cleanliness class.
- Microbial Monitoring: Airborne and surface microbial samplers detect bacteria, fungi, and other microorganisms. Regular microbial sampling verifies that contamination control measures are effective, especially in pharmaceutical and biotechnology cleanrooms.
- Automated Data Logging: Monitoring systems with data logging capabilities automatically store and organize environmental data, providing a record for regulatory audits and supporting continuous improvement.
Advanced Technologies for Cleanroom Environmental Control
Recent advancements in cleanroom technology have introduced automated, intelligent systems that enhance environmental control. Here are some of the most effective innovations for contamination-free cleanrooms:
1. IoT-Enabled Monitoring Systems
Internet of Things (IoT) technology allows for real-time, remote monitoring and control of environmental conditions within the cleanroom.
- Remote Access: Facility managers can access real-time environmental data from any location, enabling immediate action if conditions deviate from acceptable ranges.
- Predictive Analytics: IoT-enabled systems use predictive analytics to identify trends and detect potential issues before they impact production, supporting proactive maintenance and compliance.
- Automated Alerts: IoT systems provide alerts when temperature, humidity, or particle levels deviate from target ranges, ensuring timely response to potential contamination risks.
2. UV-C Sterilization Systems
UV-C sterilization is an effective tool for neutralizing airborne microorganisms and keeping cleanrooms contamination-free.
- Air and Surface Sterilization: UV-C lights installed in HVAC systems and at entry points kill bacteria and viruses in the air, preventing microbial contamination.
- Automated Sterilization Cycles: Automated UV-C sterilization systems can be programmed to run sterilization cycles at regular intervals, ensuring that microbial levels remain within acceptable limits.
- Safe, Non-Invasive: UV-C sterilization is a non-invasive method that effectively reduces contamination without requiring direct contact or leaving residues, ideal for sensitive cleanroom environments.
3. Cleanroom Robotics
Robotic systems are increasingly used in cleanrooms to perform tasks that minimize human presence, reducing contamination risks.
- Automated Cleaning Robots: Robots equipped with HEPA filters and antimicrobial materials can clean floors and surfaces without introducing contaminants.
- Material Handling Robots: In industries like pharmaceuticals and electronics, robotic systems transfer materials within the cleanroom, reducing human interaction and contamination risks.
- Programmable for Specific Cleanroom Tasks: Cleanroom robots can be programmed to follow strict protocols, ensuring that tasks are completed precisely and consistently in sterile conditions.
Best Practices for Maintaining Cleanroom Environmental Control
Advanced environmental control systems require a structured approach to ensure they function effectively. Here are some best practices for maintaining a contamination-free cleanroom environment:
1. Regular Calibration and Maintenance
Routine calibration and maintenance of HVAC, filtration, and monitoring systems are essential for maintaining compliance.
- Scheduled Filter Replacements: Filters must be replaced according to manufacturer guidelines and usage rates to ensure continued efficiency.
- Calibrate Monitoring Systems: Temperature, humidity, and particle monitoring devices should be calibrated regularly to provide accurate readings and maintain regulatory compliance.
- Routine Inspections: Regular inspections of equipment and systems help identify and address issues before they impact cleanroom conditions.
2. Stringent Cleaning and Disinfection Protocols
Effective cleaning and disinfection protocols support contamination control by removing particles and microbes from surfaces.
- Use Cleanroom-Specific Cleaning Agents: Only approved cleaning agents that do not leave residues should be used, preventing buildup on surfaces.
- Scheduled Cleaning: Establish a cleaning schedule based on cleanroom classification and production levels. Higher-class cleanrooms may require more frequent cleaning.
- Non-Shedding Cleaning Supplies: Use lint-free wipes, sterile mops, and HEPA-filtered vacuums to prevent contamination during cleaning.
3. Implement Personnel Protocols
Personnel can introduce particles and microbes, making strict protocols essential for minimizing human-related contamination.
- Gowning and Hygiene Protocols: Require personnel to wear appropriate cleanroom attire, such as coveralls, masks, gloves, and shoe covers, to prevent particle shedding.
- Air Showers and Gowning Areas: Install air showers and designated gowning areas at entry points to remove particles from personnel and maintain cleanliness.
- Access Control: Limit the number of personnel entering the cleanroom, restricting access to essential staff only.
4. Maintain Comprehensive Documentation
Documentation is vital for tracking environmental conditions, maintenance activities, and personnel adherence to protocols.
- Environmental Records: Maintain logs of temperature, humidity, pressure, particle counts, and microbial levels. These records are essential for regulatory audits.
- Inspection and Maintenance Logs: Document all maintenance and calibration activities to verify compliance with manufacturer guidelines and regulatory standards.
- SOPs and Training Records: Keep detailed records of personnel training and Standard Operating Procedures (SOPs), ensuring that all staff follow proper protocols.
Advantages of Advanced Environmental Control in Cleanrooms
Implementing advanced environmental control systems in cleanrooms provides several benefits:
- Enhanced Product Quality: Effective environmental control prevents contamination, ensuring product quality and safety.
- Regulatory Compliance: Advanced monitoring and control systems support compliance with ISO, GMP, and FDA standards, reducing the risk of regulatory penalties.
- Improved Operational Efficiency: Minimizing contamination-related disruptions allows for streamlined production, reducing rework and associated costs.
- Increased Scalability: Modular environmental control systems allow cleanrooms to adapt to changing production demands, facilitating scalability and expansion.
Why Choose Wise Link for Cleanroom Environmental Control Solutions
At Wise Link, we specialize in advanced cleanroom environmental control solutions tailored to your industry’s specific needs. Our expertise ensures that your cleanroom achieves and maintains contamination-free conditions, supporting quality, efficiency, and regulatory compliance.
- Custom Environmental Control Designs: We provide tailored air filtration, HVAC, and monitoring solutions to meet the cleanliness requirements of your cleanroom.
- Cutting-Edge Technology: Wise Link integrates the latest technologies, including IoT-enabled monitoring, UV-C sterilization, and robotic systems, to ensure comprehensive contamination control.
- Experienced Support and Maintenance: Our team offers installation, calibration, and ongoing support, ensuring your cleanroom maintains optimal environmental control.
Achieving Contamination-Free Conditions with Advanced Environmental Control
Advanced cleanroom environmental control systems are essential for industries requiring sterile, contaminant-free conditions. By implementing high-efficiency filtration, precise HVAC control, real-time monitoring, and robotic assistance, cleanrooms can achieve high standards of cleanliness, supporting product integrity and regulatory compliance.
If you’re looking to upgrade or design a contamination-free cleanroom, Wise Link provides innovative solutions to meet your environmental control needs. Contact us today for a free consultation and custom quote to learn more about our cleanroom environmental control systems.
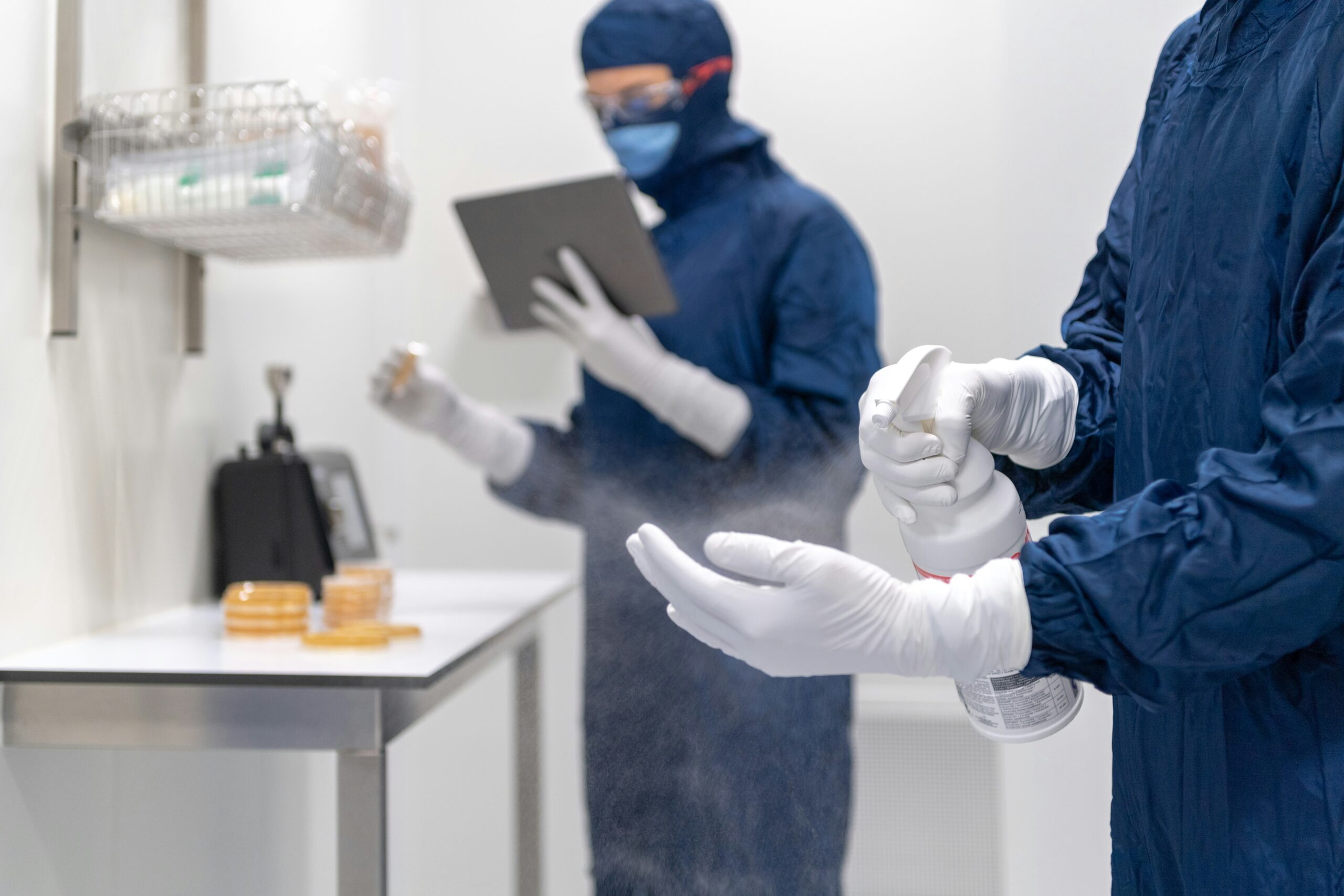
Achieve Contamination-Free Conditions with Advanced Environmental Control
Ensure Cleanliness, Compliance, and Efficiency in Your Cleanroom with Wise Link’s Expert Solutions. Contact Us Today for a Free Consultation and Custom Quote!