The Importance of Cleanroom Certification and Compliance: A Step-by-Step Guide
In the pharmaceutical industry, maintaining a controlled, sterile environment is paramount. Cleanrooms are essential for ensuring the safety, quality, and effectiveness of pharmaceutical products. However, achieving and maintaining cleanroom standards is not as simple as installing the right equipment. It requires a deep understanding of certifications, compliance regulations, and continuous monitoring to meet international standards such as GMP (Good Manufacturing Practice), ISO, and WHO.
In this comprehensive guide, we will walk through the importance of cleanroom certification and compliance in the pharmaceutical sector, outlining the step-by-step process to achieve certification, and how Smart Cleanroom Systems can streamline this process. We’ll also explore how Wise Link’s modular cleanroom solutions and integrated services can help you achieve optimal results with minimal disruption.
What is Cleanroom Certification and Why Does It Matter?
Cleanroom certification is the process by which a cleanroom is tested and verified to meet specific cleanliness standards that are critical for certain industries, particularly pharmaceuticals, biotechnology, healthcare, and food processing. These standards are set by regulatory bodies such as the FDA, WHO, and ISO, and they dictate the acceptable levels of airborne particles, temperature, humidity, and other factors that could affect the cleanliness and sterility of the environment.
In the pharmaceutical industry, maintaining compliance with these standards is not just a regulatory requirement; it is essential for ensuring product quality, patient safety, and regulatory approval. A certified cleanroom ensures that all processes within the room—whether it’s the manufacturing of medications or the packaging of medical devices—are carried out in an environment that minimizes contamination risks.
Types of Cleanroom Certifications and Compliance Standards
The certification process can vary depending on the location and specific industry, but the pharmaceutical sector is subject to rigorous global standards. Here are the key certifications and compliance standards for cleanrooms:
1. GMP (Good Manufacturing Practice)
GMP is the cornerstone of cleanroom certification in the pharmaceutical industry. GMP guidelines ensure that products are consistently produced and controlled according to quality standards. This includes controlling factors such as environmental conditions, personnel hygiene, equipment calibration, and raw material quality. Pharmaceutical companies must maintain a certified cleanroom to ensure their products meet these standards.
2. ISO 14644-1
ISO 14644-1 specifies the classification of air cleanliness in cleanrooms based on the concentration of airborne particles. For pharma companies, ISO compliance ensures that the cleanroom meets the necessary cleanliness level for the production of drugs and medical devices.
3. WHO Guidelines
The World Health Organization (WHO) provides comprehensive guidelines for pharmaceutical cleanrooms, especially for facilities involved in manufacturing sterile medicines. Compliance with WHO guidelines ensures that cleanrooms maintain rigorous environmental controls and sterility for the production of critical pharmaceutical products.
Step-by-Step Guide to Cleanroom Certification and Compliance
Achieving cleanroom certification involves several key stages, from planning and design to testing and ongoing monitoring. Below is a detailed, step-by-step guide to achieving certification for your pharmaceutical cleanroom.
Step 1: Design and Planning
The first and most crucial step in achieving cleanroom certification is the design and planning phase. A cleanroom is a complex system of controlled environments, and designing it requires knowledge of airflow, particle containment, and material selection.
Wise Link’s Smart Cleanroom Systems play a crucial role in this step. With over 15 years of experience in manufacturing modular cleanroom panels and systems, Wise Link offers customized cleanroom solutions that are designed to meet stringent pharmaceutical standards. Their modular cleanroom panels—which include EPS, PU, Rockwool, and PIR sandwich panels—are ideal for pharmaceutical cleanrooms that need to meet high-quality air cleanliness standards and ensure rapid installation.
Key Considerations during the Design Phase:
- Space Planning: Ensure the layout optimizes airflow and minimizes contamination risks.
- Material Selection: Choose materials that are easy to clean and resistant to contamination.
- HVAC System Integration: HVAC systems are essential for controlling temperature, humidity, and air cleanliness.
Step 2: Installation of Cleanroom Components
Once the design is finalized, the next step is the installation of cleanroom components. The installation process must adhere strictly to the planned design, ensuring that every element—from air filtration systems to cleanroom panels—is installed according to regulatory standards.
Wise Link’s modular cleanroom panels and customized cleanroom solutions offer fast, efficient installation without compromising on quality. Their integrated cleanroom facilities and pass boxes (both with and without interlocks) help streamline installation while maintaining the required standards of cleanliness.
Step 3: Testing and Validation
After installation, the cleanroom must undergo rigorous testing and validation to ensure it meets all regulatory standards. This process includes:
- Airborne Particle Testing: Testing for the level of particulate matter in the air.
- Pressure Differentials: Ensuring that air flows in the correct direction (from clean to less clean areas).
- Air Change Rate: Verifying that the cleanroom maintains the required air exchange per hour.
- Temperature and Humidity: Ensuring the environmental controls meet the required specifications for pharmaceutical production.
At this stage, Wise Link’s cleanroom testing services can support your facility by providing testing solutions that ensure your cleanroom meets ISO, GMP, and other regulatory standards.
Step 4: Certification by Regulatory Bodies
Once the cleanroom has passed testing and validation, it is ready for certification by the relevant regulatory bodies. The certification process involves submitting your cleanroom data and documentation to the governing authority, such as the FDA, ISO, or WHO.
Wise Link’s Smart Cleanroom Systems are designed to simplify this process. By adhering to ISO 9001 standards for quality control and modular design, Wise Link ensures that your cleanroom systems are built to meet or exceed certification requirements.
Step 5: Ongoing Monitoring and Maintenance
Achieving cleanroom certification is not a one-time event. It requires ongoing monitoring and maintenance to ensure compliance over time. Regular testing, cleaning, and maintenance are essential to maintain air cleanliness and ensure that the cleanroom continues to meet GMP, ISO, and WHO guidelines.
Wise Link’s maintenance services can provide ongoing support to ensure that your cleanroom remains compliant. They also offer customized solutions for cleanroom air filtration systems and cleanroom equipment, ensuring that you always have the right tools in place for proper monitoring.
How Wise Link’s Smart Cleanroom Systems Can Help
Wise Link has built a reputation as a leader in cleanroom manufacturing, providing modular cleanroom solutions tailored to the pharmaceutical industry’s strict needs. Their integrated systems ensure rapid installation, ease of maintenance, and compliance with the highest industry standards.
Some of the key products and services Wise Link offers include:
- Cleanroom Panels: Designed with EPS, PU, Rockwool, and PIR materials to meet GMP and ISO standards.
- Pass Boxes and Doors: Custom cleanroom pass boxes, including dynamic pass boxes and high-level stainless steel pass boxes, for seamless transitions between clean and non-clean areas.
- Modular Cleanroom Systems: Wise Link specializes in modular cleanroom systems that are customizable to fit your pharmaceutical production needs.
- HVAC Systems and Air Filtration: Complete HVAC solutions for regulating temperature, humidity, and particle control.
- Ongoing Testing and Validation: Assistance with cleanroom testing, from airborne particle counting to pressure and airflow testing.
By choosing Wise Link’s smart cleanroom systems, you ensure that your cleanroom meets the highest standards of cleanliness, efficiency, and compliance, while also benefiting from fast and cost-effective installation.
Achieving cleanroom certification and compliance is a critical aspect of maintaining pharmaceutical product quality, patient safety, and regulatory adherence. By following the steps outlined in this guide and leveraging Wise Link’s modular cleanroom systems, pharmaceutical companies can ensure that their cleanrooms are designed, installed, and maintained to meet or exceed industry standards.
If you are looking for reliable, customizable cleanroom solutions, Wise Link offers the experience, expertise, and product offerings you need to succeed. Their smart cleanroom systems are designed to optimize your facility’s performance, ensuring compliance with GMP, ISO, and WHO guidelines, all while maintaining the highest level of cleanliness and efficiency.
For more information on how Wise Link can help with your cleanroom certification and compliance needs, contact us today!
Contact Us Today for Custom Cleanroom Solutions
Whether you’re building a new facility or upgrading an existing one, Wise Link is your trusted partner for smart cleanroom systems in the pharmaceutical industry. Get in touch with us to learn more about our products and services and take the first step towards achieving cleanroom certification today.
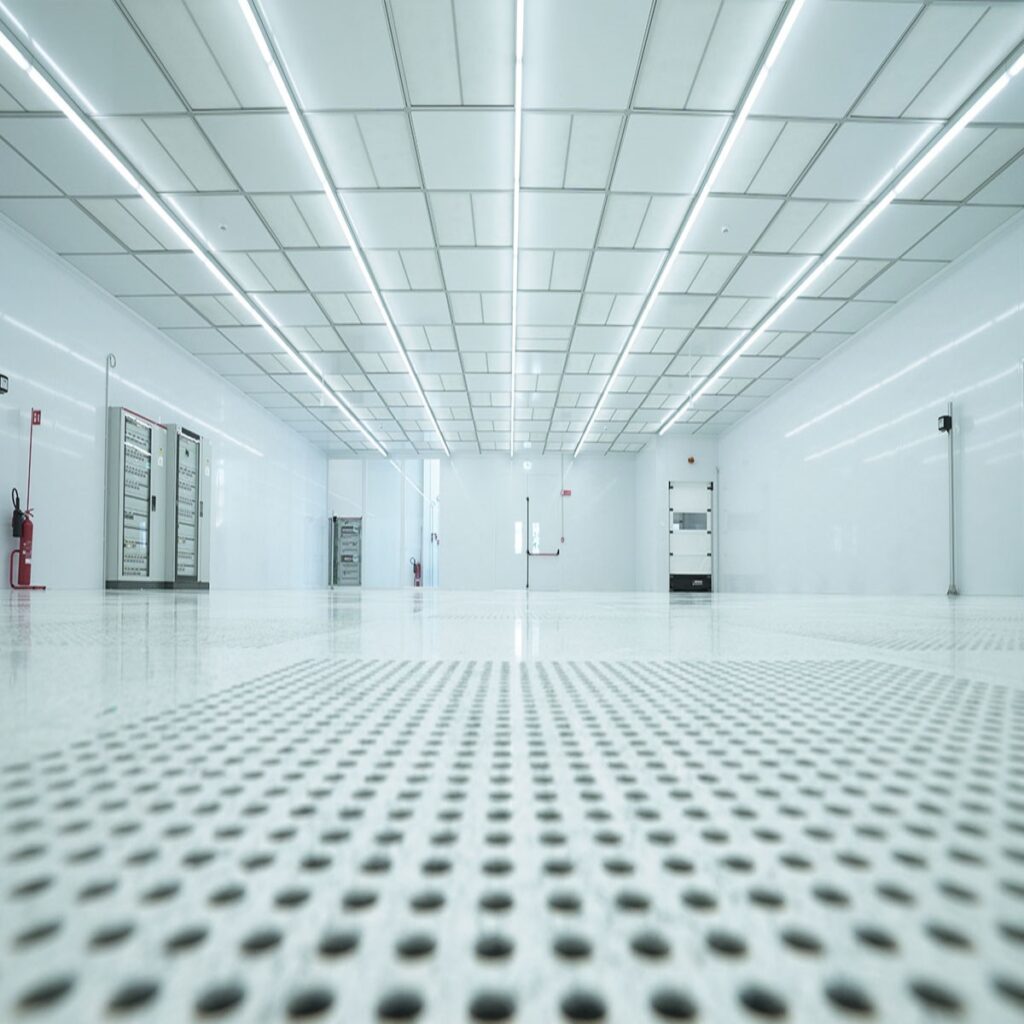