Cleanroom Maintenance Protocols for Optimal Efficiency
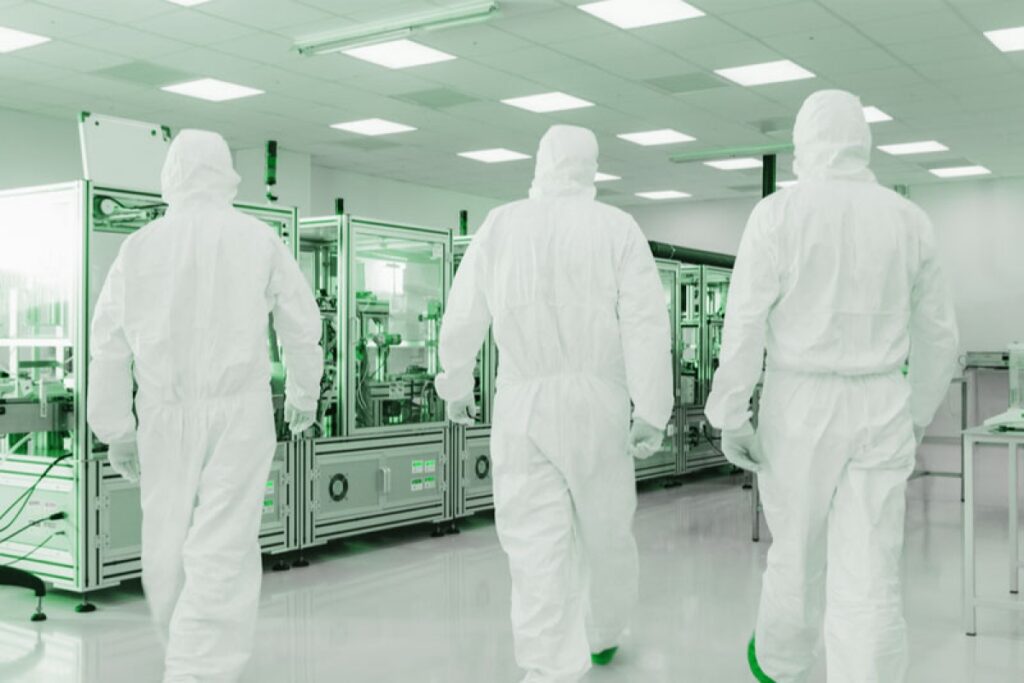
When it comes to cleanrooms, efficiency, and reliability are paramount. Whether you’re in pharmaceuticals, aerospace, biotechnology, or electronics, cleanrooms provide the controlled environment necessary for the production of sensitive products. However, the success of a cleanroom operation relies not only on its design and construction but also on the ongoing maintenance protocols that keep it running at optimal efficiency. This is where cleanroom maintenance becomes crucial.
In this blog, we’ll explore cleanroom maintenance protocols that ensure optimal performance and long-term reliability. We’ll delve into how Wiselink Group handles cleanroom upkeep and why we’re a trusted partner for businesses seeking to maintain their cleanroom environments in the most efficient manner possible.
Why Cleanroom Maintenance is Crucial for Efficiency
Maintaining a cleanroom isn’t just about cleanliness—it’s about ensuring a consistent and reliable environment where contamination is minimized, and product integrity is guaranteed. Failure to properly maintain a cleanroom can result in equipment failure, compromised air quality, and—ultimately—product contamination. For businesses in industries like pharmaceuticals, aerospace, or food production, the consequences can be dire.
Key Areas Affected by Poor Cleanroom Maintenance
- Contamination Risks: Poor maintenance of filters, HVAC systems, and cleaning protocols increases the risk of contamination.
- Operational Downtime: If a cleanroom isn’t maintained correctly, it can cause significant downtime, affecting production schedules and delivery timelines.
- Compliance Issues: Cleanrooms, especially those in industries like pharmaceuticals and biotechnology, must comply with stringent regulations. Improper maintenance can result in non-compliance, jeopardizing production.
At Wiselink Group, we understand the importance of keeping cleanrooms operating at peak performance. Our cleanroom maintenance schedule ensures that everything from air filtration to temperature control is functioning efficiently, adhering to industry regulations.
The Importance of Cleanroom Maintenance Schedules
A structured and consistent cleanroom maintenance schedule is essential to ensure the continuous and reliable operation of a cleanroom. Without a scheduled approach, critical maintenance tasks may be overlooked, leading to equipment failure and reduced cleanroom performance.
Components of a Cleanroom Maintenance Schedule
Air Filtration System Maintenance
- Cleanroom filtration systems play a central role in maintaining air quality and particle control. Regular inspections and filter changes are necessary to ensure the system operates optimally.
- Wiselink Group ensures that filtration systems are serviced according to the manufacturer’s guidelines, and particles are tested regularly to meet ISO cleanroom standards.
HVAC System Checks
- The HVAC system (Heating, Ventilation, and Air Conditioning) is integral to maintaining airflow and temperature control. Regular HVAC maintenance prevents failure and ensures the temperature, pressure, and humidity stay within specified parameters.
- Scheduled HVAC checks are conducted to clean ducts, inspect equipment, and calibrate systems to keep your environment optimal.
Cleanroom Surface Cleaning
- Surfaces inside the cleanroom must be cleaned regularly to prevent contamination. This includes floors, walls, and ceilings, all of which must be wiped down with suitable cleaning agents.
- Best practices for cleanroom surface cleaning involve the use of non-shedding materials and specific disinfectants that maintain sterility without leaving residue behind.
Equipment Calibration and Servicing
- All equipment in the cleanroom, from particle counters to temperature monitors, must be calibrated regularly. Wiselink Group provides regular equipment servicing to ensure your cleanroom remains reliable.
- This is a critical maintenance step to ensure the accuracy and functionality of instruments used in cleanroom operations.
Monitoring and Control Systems
- Cleanrooms often employ monitoring systems to track critical parameters like temperature, humidity, and particle count. These systems need regular maintenance to ensure their accuracy.
- Wiselink Group’s cleanroom maintenance protocols include regular system updates, software checks, and sensor calibrations to keep monitoring tools fully operational.

Cleanroom Upkeep: Best Practices for Longevity and Performance
When it comes to cleanroom upkeep, having a systematic approach is essential. At Wiselink Group, we follow industry-leading practices that ensure each cleanroom operates at its highest level of efficiency.
Best Practices for Cleanroom Upkeep
Scheduled Inspections
- Regular inspections are one of the best ways to detect problems before they escalate. These inspections cover everything from air quality to equipment functioning, ensuring that all elements of the cleanroom are in optimal condition.
- Wiselink Group provides comprehensive inspection services and detailed reports that help our clients stay on top of their cleanroom needs.
Cleaning Protocols
- Cleaning is a fundamental part of maintaining any cleanroom. However, specific protocols must be followed to ensure that cleaning doesn’t inadvertently introduce contaminants. For example, Wiselink Group recommends using sterile wipes, and cleaning agents that are free from residues.
- A cleanroom maintenance checklist can be created to monitor daily, weekly, and monthly cleaning tasks, ensuring that no part of the cleanroom is overlooked.
Air Quality Monitoring
- Cleanroom air must be constantly monitored for particulate matter, microbial contamination, and other factors that could impact the integrity of sensitive materials. Air quality should be measured using particle counters and microbial air samplers to meet the cleanroom’s classification.
- Wiselink Group provides real-time air quality monitoring services, ensuring compliance with all ISO 14644 standards, which regulate air cleanliness levels.
Training and Documentation
- Maintenance staff and cleanroom operators must be adequately trained in the specific protocols required to maintain a cleanroom. This includes understanding proper cleaning techniques, wearing appropriate protective gear, and following the correct maintenance schedule.
- Wiselink Group offers training programs for your staff to ensure that they understand the nuances of cleanroom reliability and the most effective ways to maintain the environment.
Maintaining Compliance: How Wiselink Group Helps You Meet Regulations
Cleanrooms, especially in regulated industries like pharmaceuticals and biotechnology, must comply with strict regulations to maintain their operational standards. Wiselink Group’s cleanroom maintenance services are designed to help you meet all relevant compliance standards.
GMP and FDA Standards for Cleanroom Maintenance
- Good Manufacturing Practice (GMP) standards require that cleanrooms are regularly maintained to ensure they are free from contamination. This includes ensuring that air filtration systems, temperature control, and cleaning protocols adhere to GMP guidelines.
- Wiselink Group ensures that all cleanrooms we design and maintain meet these regulatory requirements, ensuring continuous compliance with FDA and other relevant standards.
ISO 14644 and Cleanroom Classifications
- Cleanrooms must also adhere to ISO 14644 standards, which classify cleanrooms based on the particle count per cubic meter of air. To maintain these classifications, regular maintenance is required to ensure that systems like air filtration and HVAC are working optimally.
- Wiselink Group provides all the tools and expertise necessary to keep your cleanroom aligned with ISO standards, ensuring that air cleanliness levels and other requirements remain within acceptable ranges.
Maximizing Cleanroom Reliability with Wiselink Group’s Maintenance Services
At Wiselink Group, we understand that maintaining the efficiency and reliability of cleanrooms is key to the success of your operations. With our experience in designing, installing, and maintaining cleanrooms, we offer comprehensive maintenance solutions that not only optimize performance but also extend the lifespan of your cleanroom systems.
Tailored Maintenance Plans
We work with each client to develop a customized cleanroom maintenance schedule that aligns with their operational needs and industry standards. Whether you need daily, weekly, or monthly maintenance, Wiselink Group ensures that your cleanroom is always operating at its best.
24/7 Monitoring and Support
To ensure that your cleanroom is always at peak performance, we provide 24/7 monitoring and support. Our systems automatically detect any discrepancies in air quality or environmental conditions, alerting you before a minor issue becomes a costly problem.
Cleanroom Maintenance for Continued Success
Efficient and reliable cleanroom maintenance is not only essential for operational success but also crucial for ensuring compliance, preventing contamination, and extending the life of cleanroom equipment. At Wiselink Group, we offer a comprehensive approach to cleanroom upkeep, providing customized solutions, industry expertise, and cutting-edge technologies to keep your cleanroom environment at its best.
By partnering with Wiselink Group, you can ensure that your cleanroom operations are always aligned with the highest industry standards, providing you with peace of mind and a contamination-free production process.