China Sandwich Panel Production Line
Are you looking for a reliable China sandwich panel production line? Here we are one of the leading sandwich panel manufacturers, with the excellent ability and big capacity to provide the top-rated sandwich panels for your projects. For more, please feel free to quote us now to get sandwich panel samples.

continuous PU sandwich panel production line
We have the continuous PU sandwich panel production line, with advanced manufacturing technology with innovation, and we are aiming to provide the top-rated sandwich panels to support your local business.
Main Technical Parameters / Specifications of Continuous Sandwich Panel Production Line
Here’s an example of a table outlining the main technical parameters and specifications of a continuous sandwich panel production line:
Parameter | Description |
---|---|
Production Speed | 3-15 meters per minute (adjustable) |
Panel Thickness Range | 50mm – 200mm (customizable) |
Panel Width Range | 600mm – 1200mm (customizable) |
Outer Layer Material | Steel (galvanized, pre-painted), aluminum, etc. |
Core Material Options | Polyurethane foam, Expanded Polystyrene (EPS), Mineral Wool, etc. |
Adhesive Application | Roller or spray system |
Roll Forming Machine | Configurable for various profiles and thicknesses |
Pressing System | Double-belt press with temperature and pressure control |
Cutting Method | Flying saw or reciprocating saw |
Edge Banding/Profiling | Optional, based on customer requirements |
Control System | PLC (Programmable Logic Controller) with touchscreen interface |
Energy Consumption | Energy-efficient design with adjustable settings |
Quality Control Measures | Thickness measurement, profile inspection, bonding quality checks |
Stacking and Packing System | Automatic stacking with conveyor belt and packaging station |
Operator Interface | User-friendly interface for monitoring and adjustments |
Customization Options | Ability to customize panel dimensions, profiles, and materials |
Overall Dimensions | Varies based on specific configuration and production capacity |
Note: The values provided in the table are for illustrative purposes and may vary based on the specific manufacturer and model of the continuous sandwich panel production line. Actual specifications should be obtained from the equipment supplier.
ePS sandwich panel production line
An EPS (Expanded Polystyrene) sandwich panel production line is a manufacturing system, that is designed to produce EPS sandwich panels using EPS foam as the core material. Sandwich panels are composite materials typically used in construction for walls, roofs, and other applications due to their excellent thermal insulation properties. For more about EPS sandwich panel production, EPS cement sandwich panel production line, please feel free to contact us now.
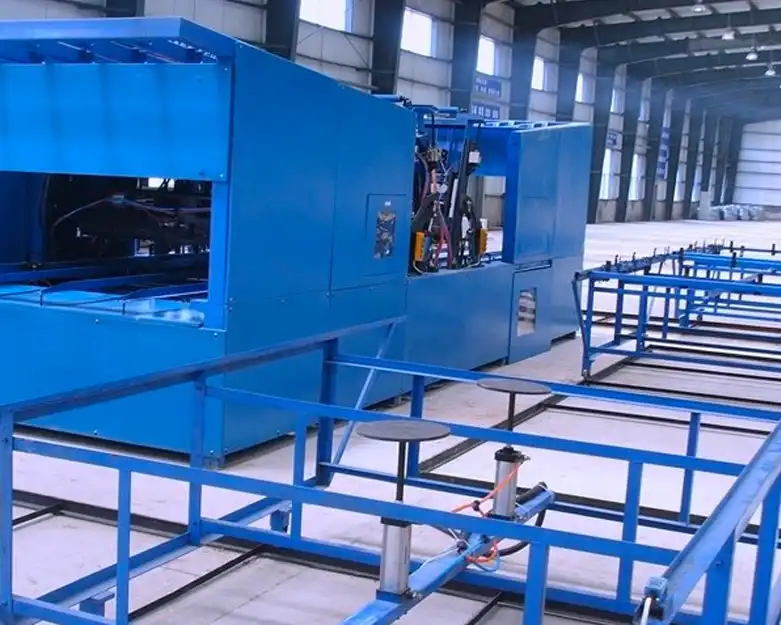

polyurethane sandwich panel production line
A polyurethane (PU) sandwich panel production line is a manufacturing system designed to produce PU sandwich panels using polyurethane foam as the core material. Polyurethane sandwich panels are widely used in the construction industry for their excellent thermal insulation and structural properties. Welcome to contact us to know more about our PU sandwich panel production line.
mineral wool sandwich panel production line
A mineral wool sandwich panel production line is a manufacturing system designed to produce sandwich panels using mineral wool as the core material. Mineral wool sandwich panels are known for their excellent fire resistance and thermal insulation properties, making them suitable for a variety of applications in the construction industry.
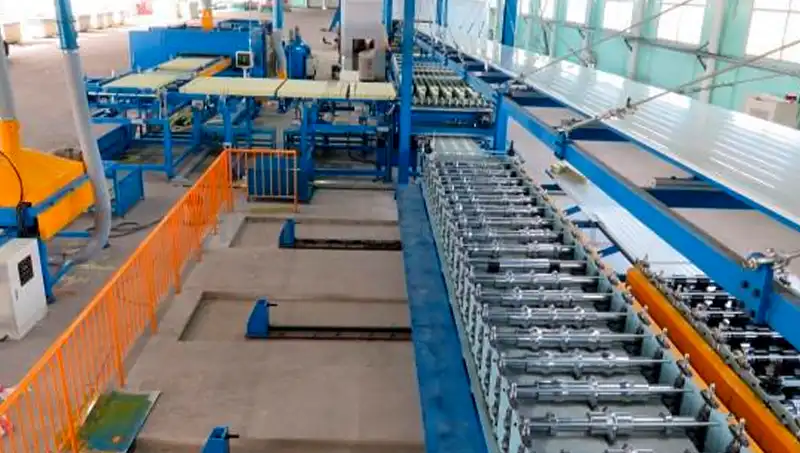
Working process of sandwich panel production line manufacturing
The working process of a sandwich panel production line involves several stages, from the handling of raw materials to the final packaging of the finished panels.
Here’s a simplified table outlining the key steps in the sandwich panel production line manufacturing process:
Step | Description |
---|---|
Step 1. Raw Materials Handling | – Steel Coils: Uncoiled and fed into the production line. |
– Core Material: Prepared for application (e.g., polyurethane foam). | |
– Adhesives: Prepared for bonding the layers. | |
Step 2. Roll Forming | Steel coils shaped into desired profile by roll forming machine. |
Step 3. Core Material Application | Core material placed between formed outer layers. |
Step 4. Pressing and Bonding | Assembled layers move through pressing machine for bonding. |
Step 5. Cutting | Continuous panel cut into individual lengths. |
Step 6. Optional Processes (Edge Banding/Profiling) | Optional steps for additional panel customization. |
Step 7. Quality Control | Thickness measurement, profile inspection, bonding quality checks. |
Step 8. Stacking and Packing | Finished panels stacked and packed for transportation. |
Step 9. Control System Monitoring | PLC with touchscreen interface oversees the process. |
Step 10. Customization and Adjustments | Operators make adjustments for panel dimensions and profiles. |
Step 11. Energy Efficiency | Some lines incorporate energy-efficient technologies. |
Step 12. Operator Interface | Operators interact with the control system for oversight. |
Note: This table provides a broad overview of the production process, and the actual steps and details can vary based on the specific design and configuration of the sandwich panel production line. The values and descriptions in the table are for illustrative purposes.
What is sandwich panel production line
A sandwich panel production line is a manufacturing system designed to produce sandwich panels, which are composite materials typically used in construction for various applications such as walls, roofs, and flooring. Sandwich panels consist of a core material, which provides insulation or structural support, sandwiched between two outer layers. The outer layers are commonly made of metal (such as steel or aluminum), but they can also be composed of other materials.
What are the main components of a sandwich panel production line?
The main components include raw material handling systems, a roll forming machine, a core material application system, pressing and bonding equipment, cutting machinery, optional processes for edge banding or profiling, quality control measures, stacking and packing systems, and a control system with operator interfaces.
What types of core materials are used in sandwich panels?
Common core materials include polyurethane foam, expanded polystyrene (EPS), mineral wool, and sometimes materials like phenolic foam or honeycomb structures. The choice depends on factors such as insulation requirements, fire resistance, and structural considerations.
What are the applications of sandwich panels?
Sandwich panels are widely used in construction for walls, roofs, and flooring due to their excellent thermal insulation properties and structural strength. They are also used in industries such as cold storage, transportation, and modular construction.
How fast can a sandwich panel production line operate?
Production speeds can vary, but a typical sandwich panel production line can operate at speeds ranging from 3 to 15 meters per minute. The actual speed may depend on factors such as panel dimensions and the specific capabilities of the production line.
What are the customization options for sandwich panels?
Sandwich panel production lines are designed to allow for customization in terms of panel dimensions, thicknesses, profiles, and even the choice of materials. This flexibility ensures that panels can be tailored to meet specific project requirements.
Are there environmental considerations in sandwich panel production?
Some modern sandwich panel production lines incorporate energy-efficient technologies to minimize environmental impact. Additionally, the choice of core materials can impact factors such as recyclability and overall sustainability.
What is the role of the control system in the production line?
The control system, often a Programmable Logic Controller (PLC), oversees the entire production process. It monitors and controls parameters such as speed, temperature, and pressure, ensuring the production line operates within specified parameters. Operators use the interface to make adjustments and oversee the process.
Is operator training required for operating a sandwich panel production line?
Yes, operator training is essential for the optimal operation of a sandwich panel production line. Operators need to be familiar with the control system, machinery, and maintenance procedures to ensure the production line’s efficiency and the quality of the manufactured panels.