Choosing the Right Cleanroom Equipment for Your Industry
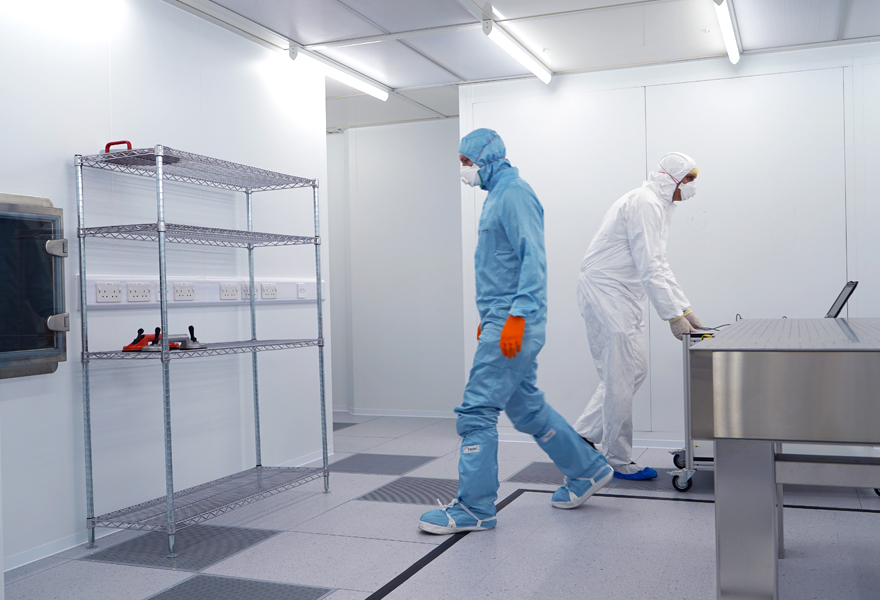
When operating in regulated industries such as pharmaceuticals, biotechnology, electronics, and aerospace, the design and operation of cleanrooms are paramount to maintaining product quality and compliance with strict industry standards. At the heart of cleanroom functionality lies the cleanroom equipment that ensures both cleanliness and operational efficiency. From cleanroom furniture to sterile workstations, and from cleanroom air showers to high-performance filtration systems, choosing the right equipment is critical for achieving optimal results.
In this guide, we explore the different types of cleanroom equipment, their functionalities, and how to select the best solutions for your specific industry needs. At Wiselink Group, we provide expert guidance and high-quality, customized solutions to meet your cleanroom requirements, ensuring you achieve top-tier performance and compliance.
Understanding the Importance of Choosing the Right Cleanroom Equipment
Cleanrooms are designed to create a controlled environment with minimal contamination, but the effectiveness of this environment depends heavily on the cleanroom equipment used. Properly selected equipment helps maintain air quality, control the temperature, and provide sterile working conditions for staff. Whether you’re working in a pharmaceutical lab, a semiconductor manufacturing facility, or a biotech research facility, the right equipment can make all the difference in achieving the desired results.
Why Cleanroom Equipment Selection Matters:
- Regulatory Compliance: Cleanrooms are often subject to strict regulations, such as GMP (Good Manufacturing Practice) for pharmaceuticals or ISO 14644 standards for air quality and cleanliness. The correct equipment is necessary to meet these standards and avoid penalties or delays in production.
- Product Quality: In industries such as pharmaceuticals or electronics manufacturing, even a small amount of contamination can compromise the quality and safety of the final product. Choosing high-quality equipment ensures that contamination is minimized, and the production process remains smooth.
- Employee Health and Safety: Cleanrooms are designed to protect both products and employees. Proper equipment, such as sterile workstations and air showers, ensures that workers are safeguarded from exposure to contaminants while maintaining the highest operational standards.
Selecting the right cleanroom equipment isn’t just about meeting regulatory standards; it’s also about ensuring the long-term efficiency, safety, and quality of your operations. Wiselink Group provides industry-specific expertise in equipping your cleanroom with solutions that optimize your operations and uphold the highest standards of cleanliness.
Key Types of Cleanroom Equipment: A Detailed Overview
Choosing the right cleanroom equipment is essential for maintaining the integrity of your cleanroom environment. Below, we explore some of the most important categories of equipment you will encounter in a cleanroom setting, from furniture to air filtration systems, and highlight the features to consider when making a selection.
1. Cleanroom Furniture: Essential for Functionality and Cleanliness
Cleanroom furniture must meet the specific requirements of a controlled environment, including being easily cleanable and resistant to contamination. This equipment supports the work being performed in the cleanroom and ensures that contamination is not introduced through the furniture itself.
Types of Cleanroom Furniture:
- Workbenches and Desks: These should be constructed from non-porous, easy-to-clean materials such as stainless steel or laminate. Adjustable height desks or ergonomic workstations may also be required depending on the nature of the tasks being performed.
- Storage Units: Shelving, cabinets, and drawers used in cleanrooms should have sealed, non-porous surfaces to prevent dust accumulation. Transparent materials may also be preferred for easy visibility of stored items.
- Seating: Cleanroom chairs must be made from materials that are easy to disinfect, such as polyurethane or stainless steel. Some cleanrooms require specialized seating for ergonomic support, such as anti-static chairs for electronics manufacturing.
Key Considerations for Cleanroom Furniture:
- Material Compatibility: Choose furniture that is compatible with the cleaning agents used in the cleanroom.
- Ease of Cleaning: All furniture should have smooth surfaces and be free of cracks and crevices to avoid contamination buildup.
- Ergonomics: Depending on the tasks performed, ergonomic furniture can improve comfort and productivity.
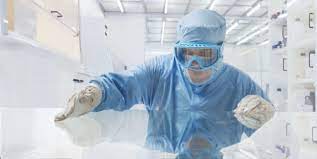
2. Sterile Workstations: Protecting Both Operators and Products
Sterile workstations are critical for operations that require precise environmental controls, such as in pharmaceuticals or biotechnology. These stations must be able to maintain sterile conditions for the entire duration of the work being performed, ensuring that products are not contaminated during preparation or handling.
Types of Sterile Workstations:
- Laminar Flow Workstations: These workstations use laminar flow to create a sterile working environment by directing filtered air over the workspace. They are commonly used in pharmaceutical manufacturing, laboratories, and research facilities.
- Biosafety Cabinets: These cabinets offer a higher level of protection, often used for handling dangerous biological substances or when working in highly controlled environments. They provide both personnel and product protection by using negative pressure and specialized filtration systems.
- Classified Workstations: Workstations are classified based on the ISO cleanroom standards (ISO 5, ISO 7, etc.), with the ISO 5 class being the most sterile and used in sensitive applications like semiconductor manufacturing.
Key Considerations for Sterile Workstations:
- Airflow Design: A well-designed laminar flow or turbulent flow system ensures that contaminants are filtered out before they can reach the workstation.
- Size and Configuration: Depending on the type of tasks performed, the workstation should be large enough to accommodate necessary equipment and materials while maintaining clean conditions.
- Ergonomics: Consider the ergonomics of the workstation to optimize employee comfort and efficiency during long periods of work.
3. Cleanroom Air Showers: Ensuring Contamination-Free Entry and Exit
Cleanroom air showers are critical equipment for preventing contamination from being introduced into a cleanroom. These showers are used as a barrier to ensure that personnel, tools, and materials are free of contaminants before entering or exiting the cleanroom.
Types of Cleanroom Air Showers:
- Standard Air Showers: These are equipped with high-velocity air jets that remove dust and particulate matter from personnel or materials before they enter the cleanroom. They are commonly found in the electronics industry and pharmaceutical facilities.
- Pass-Through Air Showers: Used for items or materials that need to pass into the cleanroom, these showers ensure that contamination is removed before they are allowed inside.
Key Considerations for Air Showers:
- Airflow Velocity: Air showers should have adjustable air velocity to ensure maximum contaminant removal without harming sensitive equipment or personnel.
- Material Durability: The construction of the air shower should be robust and resistant to the harsh chemicals and cleaning agents used in the cleanroom.
- Compliance: Ensure that the air shower meets industry standards such as ISO 14644-1 or GMP requirements for cleanrooms.
4. Cleanroom Filtration Systems: Maintaining Clean Air
Cleanroom air quality is primarily maintained through the use of advanced filtration systems that remove contaminants from the air. The cleanroom filtration system is one of the most essential pieces of equipment in a cleanroom.
Types of Cleanroom Filtration Systems:
- HEPA (High-Efficiency Particulate Air) Filters: These filters are capable of trapping 99.97% of particles as small as 0.3 microns in size. HEPA filters are commonly used in cleanrooms where the particle count must be minimized.
- ULPA (Ultra-Low Penetration Air) Filters: ULPA filters provide even finer filtration than HEPA filters, capturing 99.999% of particles as small as 0.12 microns.
- Activated Carbon Filters: Used in environments where chemical fumes or odors must be filtered out, activated carbon filters are essential for maintaining the quality of the cleanroom environment.
Key Considerations for Filtration Systems:
- Efficiency and Lifespan: Select filters with high efficiency and consider their lifespan. Regular maintenance and replacement are required to ensure continued performance.
- Airflow Rates: The airflow rates of filters should align with the required cleanroom classification.
- Noise Levels: Depending on the cleanroom’s operations, low-noise filters may be required, especially for sensitive tasks.
Why Choose Wiselink Group for Your Cleanroom Equipment?
Wiselink Group is a trusted provider of cleanroom equipment and solutions, offering a comprehensive range of high-quality products tailored to meet the specific needs of your industry. Our team of experts works closely with you to assess your cleanroom requirements, recommending the best equipment based on your specific operational needs and regulatory compliance.
We provide customized cleanroom solutions that enhance your operational efficiency and ensure your cleanroom meets the highest standards of cleanliness and safety. Whether you require cleanroom furniture, sterile workstations, or air showers, Wiselink Group is committed to delivering state-of-the-art cleanroom technology designed for maximum performance and reliability.
By choosing Wiselink Group as your cleanroom technology provider, you gain access to:
- Industry-Specific Expertise: We understand the unique requirements of different industries and provide equipment solutions that are tailored to meet these needs.
- Compliance and Certification: All our products meet the relevant ISO 14644 and GMP standards, ensuring compliance with industry regulations.
- High-Quality Equipment: Our cleanroom equipment is manufactured to the highest standards, ensuring durability, functionality, and ease of maintenance.
Selecting the right cleanroom equipment is an essential part of building a successful cleanroom that meets industry standards and ensures a contamination-free environment. With Wiselink Group’s expertise in cleanroom design, we offer a wide range of high-quality cleanroom equipment to meet the specific needs of your industry. From sterile workstations to air showers and cleanroom filtration systems, we provide the equipment you need to maintain the highest standards of cleanliness and operational efficiency.