In the realm of construction and insulation, the term “sandwich panel joint” stands as a crucial element. This article aims to delve into the intricacies of creating seamless connections in sandwich panels, offering valuable insights and expert advice for anyone involved in construction or interested in the science behind these structural wonders.
What Is Sandwich Panel Joint?
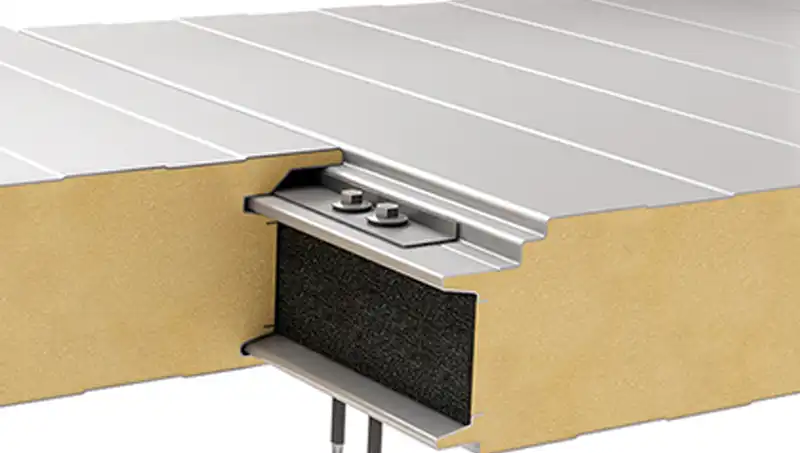
A sandwich panel joint refers to the connection or interface between two adjacent sandwich panels. Sandwich panels are composite materials typically used in construction for walls, roofs, and floors. They consist of two outer layers (skins or faces) and a core material sandwiched between them. The core material is often a lightweight, insulating material.
The joint between two sandwich panels is crucial for the overall structural integrity and performance of the panels. Properly designed joints help ensure that the panels connect securely, providing stability, insulation, and resistance to environmental factors.
There are various types of joints used in sandwich panel systems, and the specific type depends on factors such as the application, panel material, and structural requirements. Common types of joints include tongue-and-groove joints, lap joints, and interlocking joints. The goal is to create a seamless connection that maintains the structural and thermal properties of the panels.
Proper installation and sealing of joints are important to prevent issues such as air leakage, water infiltration, and heat loss. Additionally, the joint design should consider factors like expansion and contraction due to temperature variations to avoid damage or deformation over time.
A sandwich panel joint is the point where two sandwich panels meet and are connected, and it plays a crucial role in maintaining the overall performance and functionality of the panels in construction applications.
Types of Sandwich Panel Joints
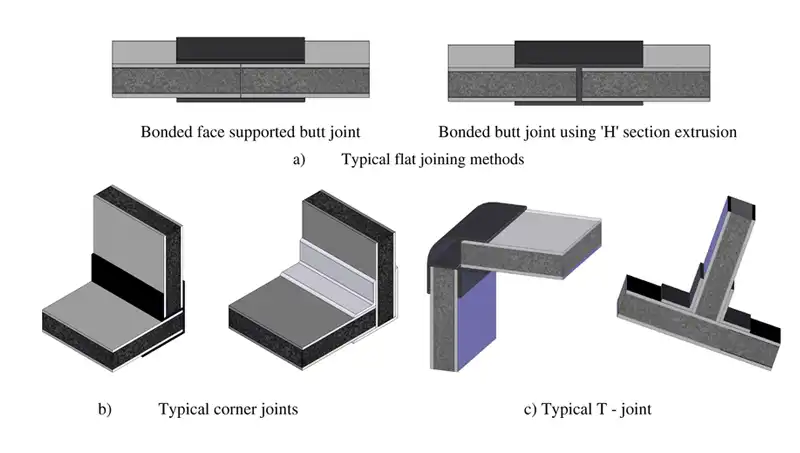
Dive into the diverse world of joint types. From tongue and groove to adhesive bonds, explore the various methods employed in creating robust sandwich panel joints. Uncover the advantages and applications of each, providing a holistic view for both novices and seasoned professionals.
There are several types of joints used in sandwich panels, each serving specific purposes and catering to different construction needs. Here are some common types:
Tongue-and-Groove Joint:
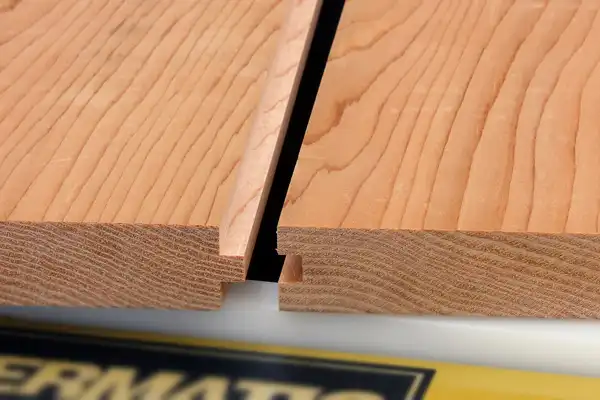
This type of joint involves a protruding “tongue” on one panel that fits into a corresponding “groove” on the adjacent panel. It provides a secure connection and helps prevent air and water infiltration.
Lap Joint:
In a lap joint, one panel overlaps the edge of the adjacent panel. It’s a simple and effective way to connect panels, providing structural stability and resistance to environmental factors.
Interlocking Joint:
Interlocking joints feature specialized shapes or mechanisms that allow panels to fit together seamlessly. This type of joint enhances structural integrity and may provide additional resistance to external forces.
Cam-Lock Joint:
Cam-lock joints involve the use of cams or wedges that are turned to lock two panels together. This type of joint is often used in modular construction for quick and easy assembly.
Butt Joint:
A butt joint is a straightforward connection where the ends of two panels meet without any overlapping or interlocking. It’s a common joint type but may require additional sealing to prevent air and water infiltration.
Metal-to-Metal Joint:
Some sandwich panels have metal skins, and the joint between them involves a connection of the metal surfaces. This can be achieved through various methods such as welding, bolting, or using specialized connectors.
Adhesive Bonding:
In addition to mechanical joints, adhesive bonding is often used to enhance the connection between panels. High-strength adhesives can improve the overall strength of the joint and create a more uniform load distribution.
Clip-and-Seal Joint:
This type of joint involves the use of clips or fasteners to secure panels together, and a sealing mechanism to prevent the ingress of water or air. It’s often used in roofing systems.
The choice of a particular joint type depends on factors like the intended use of the panels, the materials involved, and the environmental conditions the panels will be exposed to. Proper design and installation are crucial to ensure the effectiveness and longevity of the joint in a sandwich panel system.
Factors Influencing Joint Strength
Delve into the factors that impact the strength of a sandwich panel joint. From material compatibility to environmental conditions, understand how these elements play a pivotal role in determining the longevity and effectiveness of the joint.
Expert Tips for Seamless Integration
Unlock the secrets of achieving perfection in sandwich panel joints. Expert tips and tricks await as we guide you through the intricacies of ensuring a flawless integration that withstands the test of time.
Advantages of a Well-Executed Sandwich Panel Joint
Enhanced Thermal Efficiency
Explore how a properly executed joint contributes to improved thermal efficiency in structures. Learn how this small detail can make a significant impact on energy conservation and sustainability.
Structural Integrity
Discover the role of a robust sandwich panel joint in maintaining the structural integrity of buildings. Uncover the ways in which a well-crafted joint ensures stability and longevity.
FAQs:
Are sandwich panel joints suitable for all climates?
Absolutely! Sandwich panel joints are designed to withstand diverse climatic conditions, offering durability and reliability in varying environments.
How often should sandwich panel joints be inspected?
Regular inspections are recommended, with a general guideline of every 6 to 12 months. This ensures early detection of any potential issues, maintaining the structural integrity of the panels.
Can sandwich panel joints be customized for specific projects?
Indeed! Sandwich panel joints are highly adaptable, allowing for customization based on the unique requirements of each project.
Are there eco-friendly options for sandwich panel joints?
Yes, many manufacturers offer eco-friendly alternatives, promoting sustainability without compromising on performance.
What is the average lifespan of a well-maintained sandwich panel joint?
With proper maintenance, a well-executed sandwich panel joint can last for several decades, providing long-term reliability and efficiency.
Can sandwich panel joints be repaired if damaged?
In most cases, yes. Timely repairs can address minor damages, extending the lifespan of the joint and maintaining optimal performance.
Conclusion
As we conclude our exploration of the fascinating world of sandwich panel joints, it becomes evident that these seemingly small details play a monumental role in the construction industry. By understanding the nuances, exploring various joint types, and implementing expert tips, one can ensure the creation of robust, efficient structures.