In the world of modern construction and manufacturing, sandwich panels have emerged as versatile and indispensable components. These panels, consisting of a core material between two facings or skins, offer a myriad of advantages.
Let’s delve into the intricate process of sandwich panel manufacturing process and understand why it plays a crucial role in various industries.
Composition of Sandwich Panels
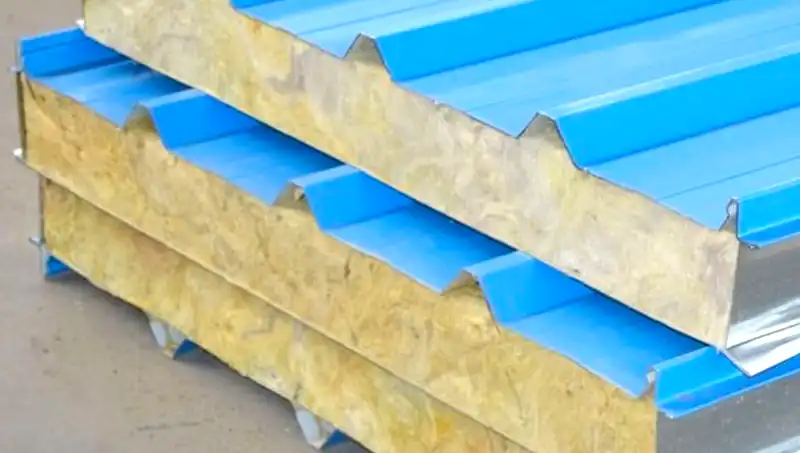
The composition of sandwich panels is a carefully orchestrated blend of materials, each playing a crucial role in determining the panel’s structural integrity, thermal performance, and overall functionality.
Core Materials:
The core of a sandwich panel serves as its backbone, providing strength and rigidity. Common core materials include:
- Foam: Polyurethane, polystyrene, and polyethylene foams are popular choices, offering lightweight properties and excellent insulation.
- Honeycomb: Made from materials like aluminum or paper, honeycomb cores provide exceptional strength-to-weight ratios.
Facings or Skins:
The facings, also known as skins, encapsulate the core and contribute to the panel’s exterior appearance. Key aspects of facings include:
- Metal Sheets: Aluminum and steel are common choices for facing materials, offering durability and corrosion resistance.
- Fiberglass: Combining strength with flexibility, fiberglass facings are prevalent in applications requiring impact resistance.
- Wood Veneer: In some cases, wood veneer facings provide a natural aesthetic while maintaining structural stability.
Adhesive Bonding:
- The adhesive used to bond the core and facings is a critical element in sandwich panel composition. It ensures a strong and durable connection between the layers. Common adhesives include epoxy, polyurethane, and phenolic resins.
Additional Reinforcements:
- Depending on the intended application, manufacturers may incorporate additional reinforcements within the core or between the core and facings. This can include materials like fiberglass or carbon fiber to enhance specific properties such as tensile strength.
Understanding the composition of sandwich panels is essential for selecting the right materials based on the desired performance characteristics. The careful balance of core materials, facings, and adhesives contributes to the overall success of these versatile panels in various industries, ranging from construction to transportation.
Benefits of Sandwich Panels
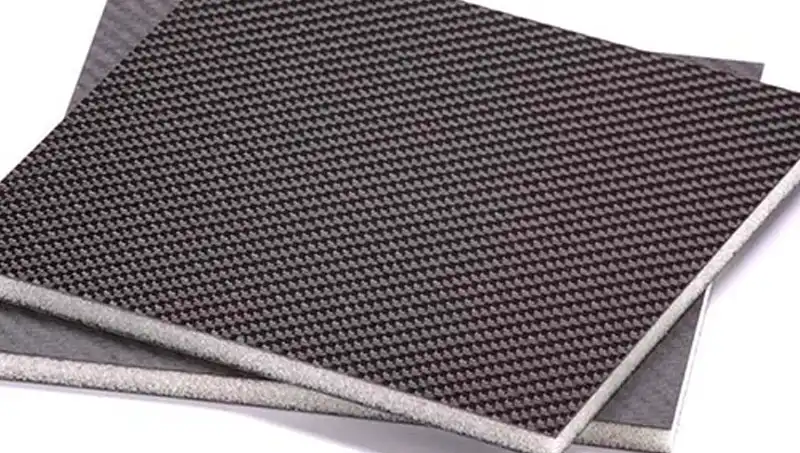
Sandwich panels offer a plethora of advantages, making them a preferred choice in diverse industries. The unique combination of core materials and facings contributes to a range of benefits that enhance their appeal for various applications.
Thermal Insulation:
One of the standout features of sandwich panels is their exceptional thermal insulation properties. The insulating core materials, such as polyurethane or polystyrene foam, create a barrier that effectively regulates temperature. This makes sandwich panels ideal for structures where energy efficiency is a priority.
Structural Strength:
Sandwich panels provide impressive structural strength while remaining lightweight. The core materials, often honeycomb or high-density foam, contribute to the panel’s ability to withstand loads and stresses. This balance between strength and weight is particularly advantageous in construction and transportation applications.
Lightweight Construction:
The lightweight nature of sandwich panels is a game-changer in industries where reducing weight without compromising strength is essential. In applications like automotive manufacturing, the panels contribute to fuel efficiency and overall performance.
Customizable Aesthetics:
With a variety of facing materials available, sandwich panels offer customizable aesthetics. Metal sheets, fiberglass, and wood veneer facings allow for a diverse range of appearances, making them suitable for architectural applications where design flexibility is crucial.
Sound Insulation:
The layered structure of sandwich panels also lends itself to effective sound insulation. This makes them valuable in applications where minimizing noise transmission is vital, such as in the construction of soundproof rooms or partitions.
Quick Installation:
Sandwich panels are known for their ease of installation. The pre-fabricated nature of these panels reduces on-site construction time, leading to cost savings and increased efficiency.
Weather Resistance:
The facing materials, especially metal sheets, provide excellent weather resistance. This ensures that sandwich panels maintain their integrity and appearance even in challenging environmental conditions, making them suitable for outdoor applications.
Cost-Efficiency:
The combination of lightweight construction, quick installation, and energy-efficient properties contributes to overall cost-efficiency. Sandwich panels offer a cost-effective solution in comparison to traditional building materials.
Versatility in Applications:
Sandwich panels find applications across various industries, including construction, automotive, cold storage, and more. Their versatility stems from the ability to tailor the composition to meet specific requirements.
Understanding these benefits highlights the multifaceted advantages that sandwich panels bring to the table. From energy savings to structural resilience, these panels continue to be a cornerstone in modern construction and manufacturing.
Continuous Panel Manufacturing Methods

Continuous panel manufacturing employs various methods to ensure a seamless and efficient production process. These methods are designed to optimize the creation of sandwich panels, providing flexibility, precision, and consistent quality.
Roller Press Method:
In this method, the core material and facing sheets are continuously fed through rollers equipped with an adhesive application system. The pressure exerted by the rollers ensures proper bonding, and the continuous movement results in a uniform panel. Roller presses are versatile and can accommodate various panel sizes.
Belt Conveyor System:
Utilizing a belt conveyor, this method involves the continuous movement of core materials and facing sheets along the production line. The adhesive is applied, and the materials are pressed together as they travel on the conveyor. This method is effective for high-volume production and allows for precise control over the panel’s dimensions.
Double-Belt Press Method:
This method involves two synchronized belts moving in opposite directions. The core material, adhesive-coated, is placed between the facing sheets, and the assembly passes through the double-belt press. The opposing movement of the belts ensures even pressure distribution, resulting in a thoroughly bonded and uniform panel.
Foaming-in-Place Process:
Particularly used for panels with foam cores, the foaming-in-place process injects the foam directly between the facing sheets. The continuous movement of the assembly ensures uniform distribution of the foam, creating panels with consistent insulation properties. This method is commonly employed in the production of insulated panels for various applications.
Rotary Press Method:
In this method, the core material is continuously fed into a rotary press, where it comes into contact with facing sheets and adhesive. The rotary motion ensures even pressure application, and the panel is cut to the desired length upon exiting the press. This method is known for its efficiency in high-speed continuous production.
Pultrusion Process:
Commonly used for producing composite sandwich panels, the pultrusion process involves pulling continuous fibers, usually fiberglass, through a resin bath and then into a shaping die. The core material is integrated during this process, resulting in a continuous, reinforced panel. This method is advantageous for applications requiring high strength and durability.
Vacuum Bagging Technique:
The vacuum bagging method involves placing the core material and facing sheets into a vacuum-sealed bag. The air is then evacuated, creating pressure that ensures proper bonding. This method is suitable for applications where a controlled environment is necessary for the curing of adhesives.
Continuous panel manufacturing methods vary based on the specific requirements of the panels and the materials used. The choice of method depends on factors such as the desired properties of the panels, production volume, and the level of automation required. Each method plays a crucial role in meeting the diverse needs of industries relying on sandwich panels for their applications.
Discontinuous Panel Manufacturing
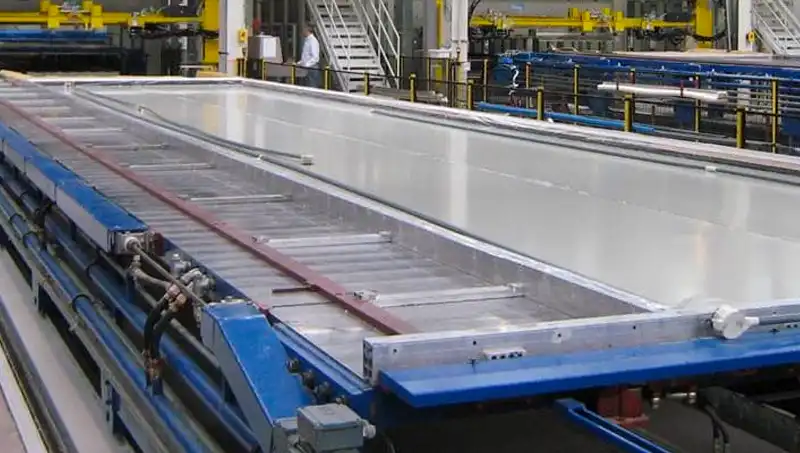
Discontinuous panel manufacturing involves a batch processing approach where panels are produced in distinct cycles, offering flexibility and customization. This method allows for more intricate control over the manufacturing parameters and is particularly suitable for applications requiring unique specifications.
Batch Processing Details:
Material Preparation:
The discontinuous manufacturing process begins with the preparation of core materials and facing sheets. These materials are cut or shaped to fit the specific dimensions required for the batch of panels being produced.
Adhesive Application:
Adhesive is carefully applied to the core material, ensuring even coverage. The type of adhesive used depends on the materials being bonded and the desired properties of the final panel.
Assembly of Components:
The core material, now coated with adhesive, is combined with the facing sheets. This assembly process can be more intricate compared to continuous manufacturing, allowing for variations in design and specifications.
Pressing and Curing:
The assembled panels undergo pressing to ensure proper bonding between the core and facing sheets. This step is followed by a curing process, allowing the adhesive to set and create a strong, cohesive structure.
Cutting and Shaping:
After curing, the panels are cut and shaped according to the specific requirements of the batch. This step allows for customization in terms of panel size, shape, and other design elements.
Quality Control:
Rigorous quality control measures are implemented at each stage of the discontinuous manufacturing process. Visual inspections, dimensional checks, and other tests ensure that the panels meet the desired standards.
Key Features and Considerations:
Flexibility and Customization:
Discontinuous manufacturing offers a high degree of flexibility, making it suitable for projects that require customized panels with unique specifications.
Variety of Materials:
This method accommodates a variety of core and facing materials, providing manufacturers with the flexibility to choose materials that best suit the intended application.
Labor Intensity:
Discontinuous manufacturing can be more labor-intensive compared to continuous processes, as each batch requires individual attention and handling.
Cost Considerations:
While it allows for customization, discontinuous manufacturing may be associated with higher production costs due to increased labor and potentially longer production cycles.
Ideal for Prototyping:
The flexibility of discontinuous manufacturing makes it ideal for prototyping and small-scale production runs, where customization and precision are paramount.
Discontinuous panel manufacturing methods cater to industries and projects where customization and intricate design details are crucial. This approach allows manufacturers to tailor panels to specific requirements, making it a preferred choice for applications that demand versatility and unique solutions.
Quality Control in Manufacturing
Quality control is a paramount aspect of sandwich panel manufacturing to ensure that the final products meet stringent standards for performance, durability, and safety. Implementing effective quality control measures is essential throughout the production process to guarantee uniformity and adherence to specifications.
Ensuring Panel Uniformity:
Material Inspection:
- Quality control begins with a thorough inspection of incoming materials. Core materials, facing sheets, and adhesives are scrutinized for compliance with specified standards. Any deviation from quality parameters can lead to rejection or rectification.
Adhesive Application Precision:
- During the manufacturing process, the application of adhesive is closely monitored. Consistent and precise adhesive application is crucial to achieving a strong bond between the core and facing sheets.
Pressing and Bonding Quality:
- The pressing phase, where the sandwich panel components are bonded together, undergoes meticulous scrutiny. Pressure levels, temperature, and pressing duration are carefully controlled to ensure optimal bonding and panel integrity.
Dimensional Checks:
- Post-production, each panel undergoes dimensional checks to verify that it meets the specified size requirements. Deviations outside acceptable tolerances are flagged for correction or rejection.
Surface Inspection:
- The surface of the panels is thoroughly inspected for defects, irregularities, or damage. This includes checks for dents, scratches, and other imperfections that might compromise the visual and structural quality of the panel.
Weight and Density Verification:
- Sandwich panels are often designed with specific weight and density requirements. Quality control measures include weighing panels to ensure they align with the intended specifications.
Adhering to Industry Standards:
Regulatory Compliance:
- Sandwich panel manufacturers adhere to industry-specific regulations and standards. Compliance with building codes, fire safety regulations, and other relevant standards is essential to ensure the panels meet safety requirements.
Testing Protocols:
- Implementing standardized testing protocols is crucial. This may include testing for thermal conductivity, fire resistance, load-bearing capacity, and other factors that align with the intended application of the panels.
Certification Processes:
- Obtaining certifications from regulatory bodies or industry associations signifies that the sandwich panels meet recognized quality and safety standards. This enhances consumer confidence and ensures the panels’ acceptance in various applications.
Implementing robust quality control measures in sandwich panel manufacturing is imperative to deliver products that meet the demands of diverse industries. From material inspection to adherence to industry standards, the emphasis on quality control contributes to the reliability and performance of sandwich panels in real-world applications.
Conclusion
In conclusion, the manufacturing process of sandwich panels is a critical aspect that influences their performance across various industries. From construction to automotive applications, these panels have proven their worth. As technology advances and sustainability becomes more prominent, the future holds exciting prospects for the world of sandwich panel manufacturing.
FAQs
Are sandwich panels only used in construction?
No, sandwich panels find applications in various industries, including automotive and cold storage.
How do manufacturers ensure the quality of sandwich panels?
Quality control measures and adherence to industry standards play a crucial role in ensuring panel uniformity.
What are the challenges faced in sandwich panel manufacturing?
Common challenges include maintaining consistency and addressing environmental concerns.
Are there eco-friendly options in sandwich panel manufacturing?
Yes, manufacturers are exploring sustainable materials and recycling processes.
What is the significance of smart panels in the future of manufacturing?
Smart panels with integrated technology are expected to revolutionize the industry by offering advanced functionalities.