The Importance of Proper Cleanroom Storage & Material Handling
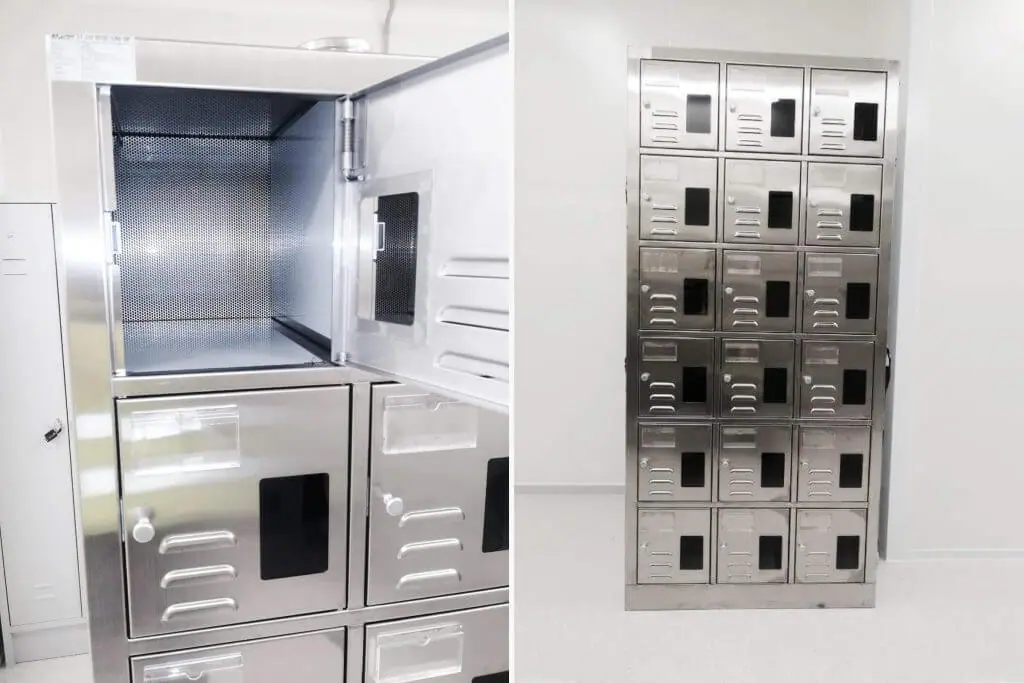
In industries where contamination can compromise the quality and safety of products, maintaining a pristine cleanroom environment is of utmost importance. For businesses operating in highly regulated sectors, such as pharmaceuticals, biotechnology, electronics, and aerospace, it is critical that every aspect of the cleanroom — including storage and material handling — is carefully managed to prevent contamination.
Proper cleanroom storage solutions and material handling systems are essential components in creating and maintaining a contamination-free environment. In this blog, we will explore why cleanroom storage is so important, how proper material handling can reduce contamination risks, and how Wiselink Group offers tailored solutions to meet GMP storage requirements and other industry standards.
Understanding the Role of Cleanroom Storage
Cleanroom storage is not just about keeping materials in a designated area; it is about ensuring that everything within the cleanroom is stored and handled in a manner that prevents contamination. The storage of equipment, tools, raw materials, and even finished products plays a crucial role in maintaining the integrity of the cleanroom environment. Improper storage practices can lead to the introduction of particulate matter, microbes, and other contaminants into the controlled environment.
Key Considerations in Cleanroom Storage:
- Temperature and Humidity Control: Many industries require specific environmental conditions for storage. Proper storage solutions include temperature-controlled units and humidity management to ensure that materials are kept in optimal conditions.
- Sealed Storage Containers: All materials in a cleanroom should be kept in sealed containers that prevent exposure to contaminants. These containers also make it easier to maintain cleanliness by allowing for effective decontamination processes.
- Organized Storage Layouts: A well-organized cleanroom storage layout is essential for reducing the likelihood of contamination. Properly labeling and categorizing materials ensures that only necessary items are present in the cleanroom at any given time.
At Wiselink Group, we specialize in providing customized cleanroom storage solutions that ensure materials are kept in the ideal conditions to minimize contamination risks. Our storage systems are designed to comply with industry standards, including GMP storage requirements, and are ideal for any industry that requires stringent control over the cleanliness of their environment.
The Significance of Material Handling in Cleanroom Environments
Material handling is another critical factor in maintaining a contamination-free cleanroom environment. The process of moving materials, tools, and products within the cleanroom should be done in a way that prevents the introduction of contaminants. This includes the use of specialized cleanroom transport systems, which are designed to protect materials from both airborne and surface contamination during transit.
The methods of material handling and the equipment used play a significant role in maintaining cleanliness. Contaminants can easily be introduced during handling if proper techniques and equipment are not employed.
Key Elements of Effective Cleanroom Material Handling:
- Cleanroom Transport Systems: These are specialized systems designed for the safe transport of materials within a cleanroom. They are designed to prevent contamination and minimize the risk of cross-contamination between different cleanroom zones.
- Automated Handling Solutions: Automated systems can improve efficiency in the cleanroom by reducing human interaction with sensitive materials, which in turn minimizes the risk of contamination.
- Specialized Equipment: The use of tools such as cleanroom trolleys, carts, and conveyors ensures that materials are safely moved from one point to another without coming into contact with potentially harmful contaminants.
Wiselink Group offers innovative cleanroom transport systems and material handling solutions that help businesses maintain a contamination-free environment. Our systems are designed to adhere to the strictest industry regulations and ensure that materials are handled with the utmost care throughout the cleanroom environment.
GMP Storage Requirements and Compliance
In industries such as pharmaceuticals and biotechnology, Good Manufacturing Practices (GMP) govern the storage, handling, and transportation of materials to ensure product quality and safety. GMP storage requirements are a critical part of the process, as they outline the conditions under which materials must be stored to prevent contamination. These requirements dictate the types of storage containers, the methods of storage, and the environmental conditions that must be maintained.
Key GMP Storage Requirements:
- Segregation of Materials: Different materials must be stored in separate areas to prevent cross-contamination. Raw materials, intermediate products, and finished goods should be stored in distinct zones to avoid mix-ups.
- Environmental Control: Cleanrooms designed for GMP compliance must meet stringent environmental conditions. This includes controlling temperature, humidity, and airflow within the storage areas.
- Labeling and Documentation: All stored materials must be clearly labeled and documented to ensure traceability. This helps prevent errors and ensures that the materials are easily identifiable when needed.
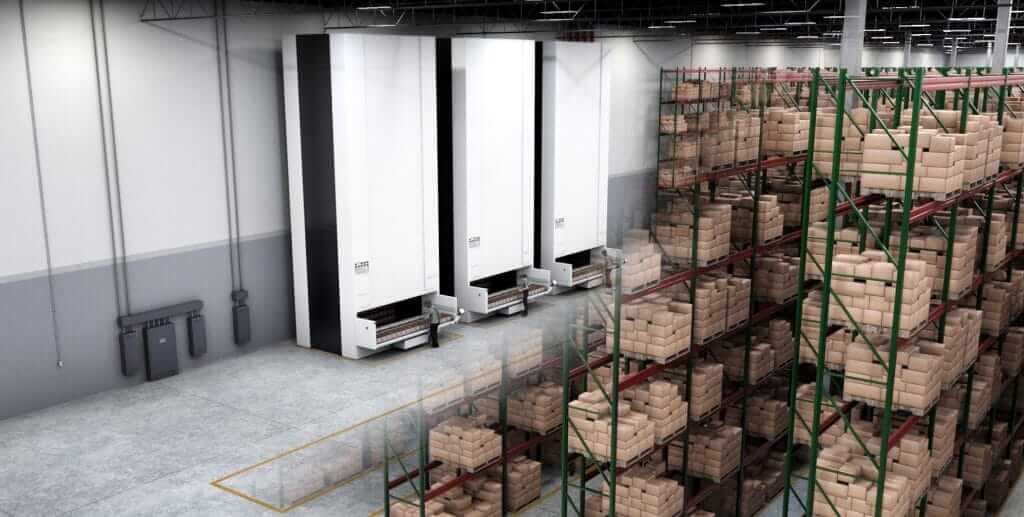
At Wiselink Group, we are experts in providing GMP-compliant storage solutions that meet the regulatory requirements of the pharmaceutical and biotechnology industries. Our storage systems ensure that your materials are kept in the correct conditions, reducing the risk of contamination and ensuring regulatory compliance.
Cleanroom Contamination-Free Logistics
Contamination-free logistics refers to the strategies and systems used to move materials in and out of the cleanroom environment without introducing contaminants. In cleanroom environments, logistics must be meticulously planned and executed to prevent the introduction of dirt, dust, or microbial agents into sensitive areas.
Logistics in cleanroom environments goes beyond just transportation; it also involves the safe handling, tracking, and management of materials throughout the entire supply chain.
Key Aspects of Contamination-Free Logistics:
- Airlocks and Barriers: Airlocks, entry barriers, and gowning areas are used to prevent contaminants from entering the cleanroom when materials are brought in or taken out.
- Sterilized Packaging: Materials that are delivered to a cleanroom must be packaged in sterile, sealed containers that maintain the integrity of the cleanroom environment.
- Specialized Transport Vehicles: Cleanroom logistics often involve the use of specialized vehicles that are designed to transport materials without contaminating them. These vehicles are cleaned regularly and equipped with HEPA filters to maintain air quality during transit.
With Wiselink Group, contamination-free logistics is built into our cleanroom material handling and storage systems. We ensure that every aspect of material transport and handling is designed to prevent contamination, helping you maintain a safe and sterile environment for your operations.
Best Practices for Cleanroom Storage & Material Handling
To ensure that your cleanroom remains contamination-free, it is crucial to follow best practices for storage and material handling. These practices not only help maintain cleanliness but also improve operational efficiency, reduce waste, and ensure regulatory compliance.
Best Practices for Cleanroom Storage:
- Regular Audits and Inspections: Conduct regular audits and inspections to ensure that storage areas are clean, organized, and compliant with GMP storage requirements.
- Use of Controlled Access: Limit access to storage areas to authorized personnel only, ensuring that contaminants are not inadvertently introduced.
- Minimize Storage in Cleanroom: Store only the materials necessary for immediate use in the cleanroom. Excess materials should be stored in designated storage areas outside the cleanroom environment.
Best Practices for Material Handling:
- Training and Education: Ensure that all personnel handling materials in the cleanroom are properly trained in contamination control practices.
- Use of Protective Equipment: Workers should use the proper cleanroom gloves, gowns, and masks to avoid contaminating materials during handling.
- Scheduled Maintenance: Regularly maintain and clean all transport equipment, including carts and trolleys, to ensure they are free from contaminants.
At Wiselink Group, we offer tailored cleanroom storage solutions and material handling systems that follow these best practices, ensuring that your cleanroom remains contamination-free and compliant with industry regulations.
The Benefits of Proper Cleanroom Storage & Material Handling
The benefits of having a robust cleanroom storage and material handling system are substantial. By implementing proper systems, businesses can reduce the risk of contamination, improve operational efficiency, ensure regulatory compliance, and protect product quality.
Key Benefits:
- Reduced Contamination Risk: Proper storage and handling systems reduce the likelihood of particulate and microbial contamination in the cleanroom.
- Increased Efficiency: Streamlined storage and material handling systems improve the workflow within the cleanroom, reducing downtime and improving productivity.
- Regulatory Compliance: Adhering to GMP storage requirements and other industry standards ensures that your cleanroom operations meet regulatory expectations.
- Improved Product Quality: Cleanrooms with effective storage and handling systems are better equipped to produce high-quality, safe products.
At Wiselink Group, we are committed to helping our clients realize these benefits by providing high-quality, custom-designed cleanroom storage solutions and material handling systems. Our systems are designed to improve your cleanroom’s efficiency, compliance, and overall performance.
Proper cleanroom storage and material handling are essential for maintaining a contamination-free environment in industries where quality, safety, and compliance are critical. With Wiselink Group’s custom cleanroom storage solutions, cleanroom transport systems, and material handling services, you can ensure that your cleanroom meets the highest standards of cleanliness, operational efficiency, and regulatory compliance. By implementing best practices in cleanroom storage and material handling, you can protect your products, reduce contamination risks, and improve overall productivity, all while maintaining a contamination-free environment that meets the demands of the most regulated industries.
Let Wiselink Group be your partner in achieving the highest level of cleanliness and efficiency in your cleanroom operations.