When it comes to construction and building materials, sandwich panels will go to your mind. But what is a sandwich panel, and why is it becoming a popular choice in various industries?
In this comprehensive guide, we’ll delve into the fascinating world of sandwich panels, covering everything from their composition and applications to their advantages and disadvantages.
What Is Sandwich Panel?
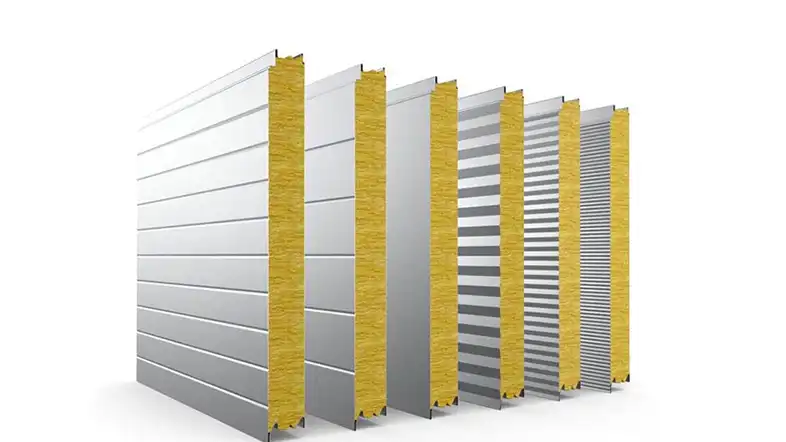
A sandwich panel is a structural material consisting of three layers – two outer layers, also known as skins, and a core material sandwiched between them. This core material can be made from various substances, including foam, metal, or even paper honeycomb. The purpose of this core is to provide stability and insulation to the panel.
What Is Sandwich Panel Made Of?
- Outer Skins: These are typically made of materials like steel, aluminum, fiberglass, or plywood, depending on the intended use of the panel.
- Core Material: The core can be made of materials such as polyurethane foam, polyisocyanurate foam, mineral wool, or expanded polystyrene (EPS).
What Is Sandwich Panel Construction
Sandwich panel construction refers to a building construction technique that involves the use of sandwich panels as structural and insulating elements.
A sandwich panel is typically composed of three layers:
- Face Sheets: These are the outer layers of the panel and are often made of materials like steel, aluminum, or other durable materials. The face sheets provide structural strength and protection to the panel.
- Core Material: The core of the sandwich panel is made of an insulating material, which can vary depending on the type of panel being used. Common core materials include Expanded Polystyrene (EPS), Polyurethane (PU), Polyisocyanurate (PIR) foam, mineral wool, and others. The core material serves as insulation and helps regulate temperature within the building.
The term “sandwich” comes from the fact that the core material is sandwiched between the two face sheets, creating a composite structure.
Sandwich panel construction offers several advantages:
- Thermal Insulation: The insulating core material provides excellent thermal insulation, helping to maintain a comfortable temperature inside the building and reduce energy consumption for heating or cooling.
- Structural Strength: The face sheets provide structural strength to the panel, allowing it to bear loads and resist deformation. This makes sandwich panels suitable for use in walls, roofs, and floors.
- Lightweight: Many core materials used in sandwich panels are lightweight, making them easy to handle and transport during construction.
- Speed of Installation: Sandwich panels are often prefabricated, which means they can be quickly and easily installed at the construction site, reducing construction time and labor costs.
- Versatility: Sandwich panels can be used in a wide range of building applications, including residential, commercial, industrial, and agricultural structures.
- Customization: Sandwich panels are available in various thicknesses, sizes, and with different face sheet materials, allowing for customization to meet specific design and performance requirements.
However, it’s important to note that the choice of core material and face sheet material can affect factors such as fire resistance, moisture resistance, and overall building performance. Local building codes and regulations should be followed when using sandwich panels in construction to ensure compliance with safety and quality standards. Additionally, proper installation and maintenance are crucial to maximize the benefits of sandwich panel construction.
What Is EPS Sandwich Panel?
An EPS sandwich panel, or Expanded Polystyrene sandwich panel, is a building material commonly used in the construction industry for its insulation and structural properties. It consists of three layers:
- Outer and Inner Face Sheets: These are typically made of materials like steel, aluminum, or other durable materials. The face sheets provide strength and protection to the panel.
- Core Material: The core of an EPS sandwich panel is made of Expanded Polystyrene (EPS) foam. EPS is a lightweight, rigid, and thermally insulating material. It is known for its excellent insulating properties, which help regulate temperature and improve energy efficiency in buildings.
The sandwich panel construction, with the EPS foam core between two face sheets, offers several advantages:
- Insulation: EPS is an effective insulator, helping to keep buildings warm in the winter and cool in the summer, which can result in energy savings and improved comfort.
- Lightweight: EPS is lightweight compared to many other building materials, making it easier to handle and transport.
- Structural Strength: The face sheets provide structural strength to the panel, allowing it to bear loads and resist bending or deformation.
- Fire Resistance: EPS foam can be treated to enhance its fire resistance properties, making EPS sandwich panels suitable for various building applications.
- Quick Installation: The panels are often prefabricated and can be quickly installed, reducing construction time.
EPS sandwich panels are commonly used in the construction of walls, roofs, and floors in commercial and industrial buildings. They are favored for their insulation properties, cost-effectiveness, and ease of installation. However, it’s important to consider local building codes and regulations when using EPS sandwich panels, as fire safety and other factors may influence their suitability for specific applications.
What is PU Sandwich Panel?
A PU sandwich panel, or Polyurethane sandwich panel, is a type of building material commonly used in construction for its insulation and structural properties. Like EPS sandwich panels, PU sandwich panels consist of three layers:
- Outer and Inner Face Sheets: These are typically made of materials like steel, aluminum, or other durable materials. The face sheets provide strength and protection to the panel.
- Core Material: The core of a PU sandwich panel is made of polyurethane foam. Polyurethane is a type of plastic material that offers excellent insulation properties. It is known for its high thermal resistance, which helps in maintaining temperature control within buildings.
The combination of these layers provides several advantages:
- Thermal Insulation: Polyurethane foam is a highly efficient thermal insulator. PU sandwich panels help in keeping buildings well-insulated, which can lead to energy savings and improved indoor comfort.
- Lightweight: Polyurethane foam is lightweight, making the panels easier to handle and transport during construction.
- Structural Strength: The face sheets provide structural strength to the panel, allowing it to support loads and resist deformation.
- Fire Resistance: PU foam can be treated to enhance its fire resistance properties, although it may not be as fire-resistant as some other materials, such as mineral wool.
- Quick Installation: PU sandwich panels are often prefabricated and can be rapidly installed, reducing construction time.
PU sandwich panels are commonly used in the construction of walls, roofs, and floors in various types of buildings, including commercial, industrial, and residential structures. They are favored for their thermal insulation capabilities, which contribute to energy efficiency, and their ease of installation.
However, as with any construction material, it’s important to consider local building codes and regulations when using PU sandwich panels to ensure compliance with safety and performance standards. Additionally, fire safety precautions may need to be taken into account when using PU panels in certain applications.
What is PIR Sandwich Panel?
A PIR sandwich panel, or Polyisocyanurate sandwich panel, is a type of building material used in construction for its excellent insulation and structural properties.
Similar to EPS and PU sandwich panels, PIR sandwich panels consist of three layers:
- Outer and Inner Face Sheets: These face sheets are typically made of materials like steel, aluminum, or other durable substances. The face sheets provide strength and protection to the panel.
- Core Material: The core of a PIR sandwich panel is made of polyisocyanurate foam. Polyisocyanurate is a type of rigid plastic foam that offers exceptional thermal insulation properties. It is highly regarded for its high thermal resistance, which helps maintain temperature control within buildings.
PIR sandwich panels offer several advantages:
- Superior Thermal Insulation: Polyisocyanurate foam is known for its outstanding thermal insulation capabilities. PIR sandwich panels help in keeping buildings well-insulated, leading to energy savings and improved indoor comfort.
- Lightweight: PIR foam is lightweight, making the panels easy to handle and transport during construction.
- Structural Strength: The face sheets provide structural strength to the panel, allowing it to support loads and resist deformation.
- Fire Resistance: PIR foam has good inherent fire-resistant properties, making PIR sandwich panels less susceptible to fire damage compared to some other insulation materials.
- Quick Installation: PIR sandwich panels are often prefabricated and can be rapidly installed, reducing construction time.
PIR sandwich panels are commonly used in the construction of walls, roofs, and floors in various types of buildings, including commercial, industrial, and residential structures. They are favored for their exceptional thermal insulation, which contributes to energy efficiency, and their ease of installation.
Nevertheless, as with any construction material, it’s crucial to consider local building codes and regulations when using PIR sandwich panels to ensure compliance with safety and performance standards. Fire safety precautions should also be taken into account when using PIR panels in certain applications.
Applications of Sandwich Panels
Sandwich panels are incredibly versatile and find applications across multiple industries. Let’s explore some of the most common uses:
Building Construction
Sandwich panels are frequently employed in the construction of walls, roofs, and floors in residential, commercial, and industrial buildings. They offer excellent thermal insulation, reducing energy consumption and maintaining comfortable indoor temperatures.
Transportation
In the automotive and aerospace industries, sandwich panels are used to construct lightweight and fuel-efficient vehicles and aircraft. The combination of strength and low weight makes them ideal for these applications.
Cold Storage
Sandwich panels with insulating cores are widely used in cold storage facilities, ensuring that temperature-sensitive goods remain at the desired temperature.
Industrial Equipment
These panels are employed in the creation of cleanrooms, partitions, and enclosures for various industrial purposes, providing durability and easy maintenance.
Advantages of Using Sandwich Panels
So, what makes sandwich panels so appealing in these diverse applications? Let’s explore their advantages:
Thermal Insulation
The core material in sandwich panels provides excellent thermal insulation properties, making them energy-efficient and cost-effective in maintaining temperature-controlled environments.
Lightweight
Compared to traditional construction materials, sandwich panels are lightweight, reducing the overall weight of structures, vehicles, or equipment.
Strength and Durability
The combination of outer skins and the core material results in a strong and durable structure that can withstand various environmental conditions.
Design Flexibility
Sandwich panels can be customized in terms of size, shape, and color, offering architects and designers a wide range of creative possibilities.
Disadvantages to Consider
While sandwich panels offer numerous benefits, they are not without their drawbacks:
Cost
High-quality sandwich panels can be expensive, especially those with specialized cores and skins.
Limited Fire Resistance
Some sandwich panels may have limited fire resistance, depending on their core material. It’s essential to choose the right type for specific applications.
FAQs
Are sandwich panels environmentally friendly?
Sandwich panels can be eco-friendly if they are manufactured using sustainable materials and production processes. Look for panels with recyclable cores and skins.
Can sandwich panels be used in extreme weather conditions?
Yes, sandwich panels are designed to withstand various weather conditions, including extreme cold and heat. However, the choice of core and skin materials should match the intended environment.
How do I maintain sandwich panels?
Maintenance of sandwich panels is relatively easy. Regular cleaning and inspection for damage or wear are usually sufficient to ensure their longevity.
Are sandwich panels suitable for residential construction?
Yes, sandwich panels are commonly used in residential construction, particularly for energy-efficient homes that require excellent insulation.
Do sandwich panels require professional installation?
While it’s possible to install sandwich panels yourself, professional installation is recommended for ensuring the panels’ proper alignment and structural integrity.
Can sandwich panels be recycled?
Yes, many sandwich panels are recyclable, making them a sustainable choice for environmentally conscious projects.
Conclusion
In conclusion, sandwich panels are a versatile and innovative construction material that offers a wide range of benefits, including thermal insulation, strength, and design flexibility. While they may come with a higher price tag and some limitations, their numerous advantages make them a compelling choice in various industries.
Whether you’re constructing a building, a vehicle, or an industrial facility, consider the advantages of sandwich panels in your next project.