Cleanroom vs. Grey Room: What’s the Difference and Why It Matters
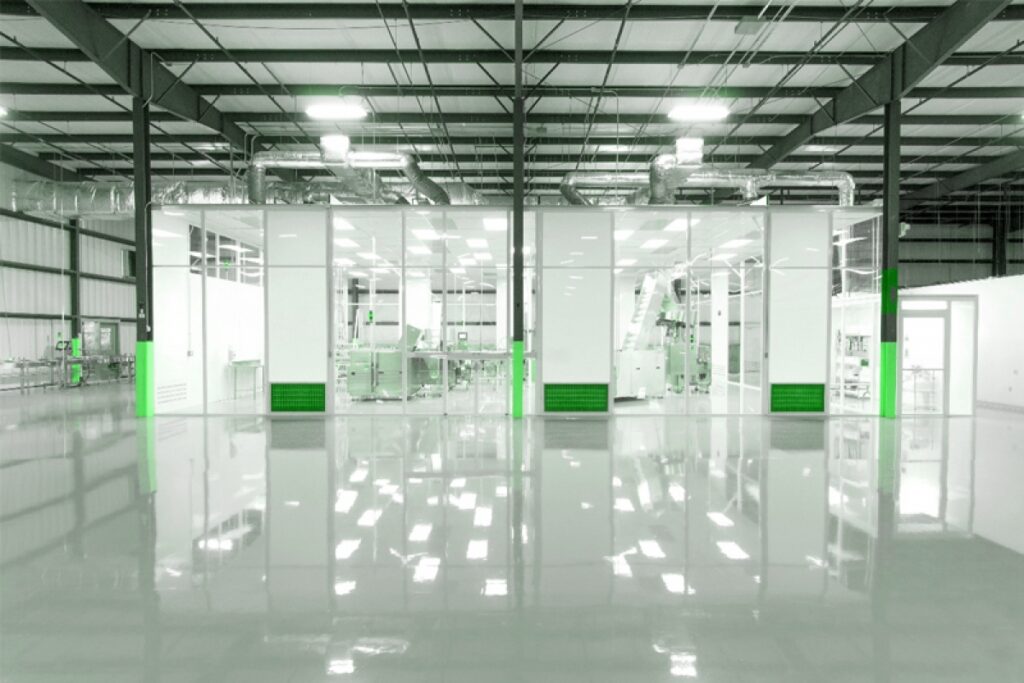
In industries such as pharmaceuticals, biotechnology, semiconductor manufacturing, and aerospace, maintaining an environment that ensures product safety, quality, and compliance is crucial. While the term cleanroom is often well-known and understood, many people may not be as familiar with the concept of a grey room. Understanding the difference between a cleanroom and a grey room is important for businesses looking to optimize their operations, adhere to cleanliness standards, and meet industry-specific requirements.
In this blog, we will provide a comprehensive cleanroom vs grey room comparison, exploring the specific functions, cleanliness standards, and operational requirements that distinguish these two types of controlled environments. We will also highlight why choosing the right environment for your industry needs is essential and how Wiselink Group offers tailored cleanroom solutions that adhere to the most stringent standards.
What is a Cleanroom?
A cleanroom is a controlled environment where contaminants, such as dust, airborne microbes, and other pollutants, are carefully managed to ensure that the processes and products within it are protected from contamination. Cleanrooms are used in industries that require ultra-clean environments, where even the slightest contamination can have a major impact on the quality or safety of the final product. Wiselink Group specializes in designing, constructing, and maintaining custom cleanroom solutions that meet the specific needs of industries like pharmaceuticals, medical devices, and semiconductor manufacturing.
Cleanrooms are classified according to cleanliness standards that determine the allowable levels of airborne particles and microbial contamination. The most widely recognized classification system is ISO 14644-1, which sets the standard for the level of particulate contamination permissible in a cleanroom environment. The cleaner the room, the lower the class number, with Class 1 being the cleanest and Class 9 the least stringent.
Key Features of Cleanrooms:
- Particle and Microbial Control: Cleanrooms are equipped with sophisticated air filtration systems, such as HEPA (High-Efficiency Particulate Air) or ULPA (Ultra-Low Penetration Air) filters, that capture airborne particles and microorganisms.
- Controlled Temperature and Humidity: To maintain the integrity of the products, cleanrooms are often equipped with HVAC (Heating, Ventilation, and Air Conditioning) systems that regulate temperature and humidity levels.
- Strict Protocols: Employees working in cleanrooms must follow stringent protocols, such as wearing special gowns and protective gear to minimize contamination from human sources.
- Regular Monitoring and Validation: Cleanrooms are subject to continuous monitoring and periodic validation to ensure compliance with industry standards.
What is a Grey Room?
A grey room, on the other hand, is a more relaxed version of a cleanroom that lacks the strict air cleanliness control and particulate management features of a traditional cleanroom. While grey rooms are designed to provide a controlled environment, they do not adhere to the same stringent cleanliness standards as cleanrooms. Grey rooms are often used in environments where contamination is less critical, or the risks associated with contamination are manageable. These rooms are suitable for applications where moderate contamination control is sufficient, but high levels of sterility are not necessary.
The term “grey room” is often used in various industries to refer to areas that fall somewhere between a cleanroom and a standard manufacturing or working environment. These rooms may still require basic environmental controls, such as ventilation and air filtration, but they generally do not meet the ISO 14644 cleanliness classifications that cleanrooms are subjected to.
Key Features of Grey Rooms:
- Lower Air Cleanliness Standards: Grey rooms typically do not meet the stringent ISO 14644 cleanroom classifications, meaning they allow for higher particle concentrations and microbial contamination.
- Less Strict Protocols: While personnel may still be required to wear protective clothing, the protocols in grey rooms are usually less stringent than those in cleanrooms.
- Basic Environmental Controls: Grey rooms often have basic ventilation and filtration systems to maintain air quality but may not include the advanced air filtration systems like HEPA or ULPA filters found in cleanrooms.
- Lower Cost: Because grey rooms have fewer requirements for air filtration, temperature, and humidity control, they are often less expensive to design, construct, and maintain than cleanrooms.
Cleanroom vs Grey Room: A Detailed Comparison
To better understand the key differences between a cleanroom and a grey room, let’s break down the comparison based on several important factors.
1. Cleanliness Standards
The most significant difference between cleanrooms and grey rooms is the level of cleanliness they provide. Cleanrooms are designed to meet strict cleanliness standards established by regulatory bodies such as the ISO 14644 and GMP (Good Manufacturing Practice). These standards define the maximum allowable levels of airborne particles and microorganisms.
- Cleanrooms: Rely on high-efficiency air filtration systems (e.g., HEPA or ULPA) to remove contaminants from the air. The air cleanliness is classified according to ISO standards, such as ISO 14644-1, and cleanrooms must meet these specifications at all times.
- Grey Rooms: Do not meet the same stringent cleanliness standards as cleanrooms. While some basic air filtration and ventilation systems may be used, grey rooms allow for higher levels of contamination.
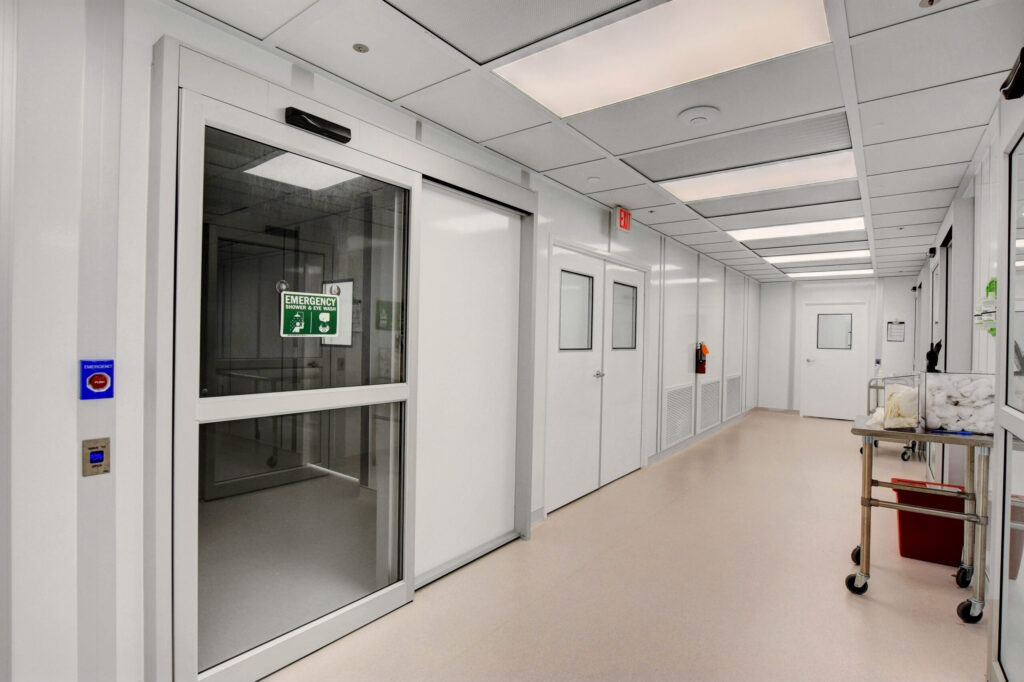
2. Air Filtration and Ventilation Systems
The quality of the air in a controlled environment is vital to preventing contamination. Cleanrooms have highly specialized HVAC systems that regulate airflow, temperature, and humidity while using HEPA or ULPA filters to ensure optimal air cleanliness. Grey rooms, in contrast, may only include basic air filtration systems, and the airflow may not be as controlled.
- Cleanrooms: Employ advanced filtration systems such as HEPA or ULPA filters that capture particles as small as 0.1 microns, ensuring high air quality and minimizing contamination risks.
- Grey Rooms: Use standard filtration systems that offer some degree of air purification but do not meet the strict standards required for cleanrooms.
3. Applications and Industries
Cleanrooms are necessary in industries where contamination could severely impact product quality, safety, or regulatory compliance. Pharmaceutical manufacturing, medical device production, semiconductor fabrication, and biotechnology are just a few examples of industries that rely on cleanrooms.
Grey rooms, however, are suitable for industries where contamination risks are lower, or where cleanliness is not as critical. General manufacturing, light assembly, and some research and development environments might use grey rooms.
- Cleanrooms: Pharmaceutical, biotech, semiconductor, aerospace, medical devices, etc.
- Grey Rooms: Electronics assembly, packaging, general industrial processes.
4. Cost and Maintenance
The cost of building and maintaining a cleanroom is typically much higher than that of a grey room. Cleanrooms require significant investment in air filtration systems, climate control systems, and regular testing and certification to ensure they meet cleanliness standards.
- Cleanrooms: High initial investment and ongoing maintenance costs for air filtration, monitoring systems, and regular validation procedures.
- Grey Rooms: Lower cost of construction and maintenance due to less stringent cleanliness requirements.
5. Regulatory Compliance
Industries that require strict regulatory compliance, such as pharmaceuticals, medical devices, and food production, often demand cleanroom environments. Failure to maintain a cleanroom that meets regulatory standards can result in fines, recalls, or even the shutdown of operations.
- Cleanrooms: Required for industries with stringent regulatory requirements, such as GMP and FDA guidelines.
- Grey Rooms: May not meet regulatory requirements for cleanliness and are not suitable for highly regulated industries.
Why the Difference Matters for Your Business
Choosing between a cleanroom and a grey room depends on your industry, the type of products you manufacture, and the level of contamination control required. The decision impacts everything from operational costs to regulatory compliance, and it is crucial for businesses to understand the distinction.
- If you operate in a highly regulated industry, such as pharmaceuticals, biotechnology, or semiconductor manufacturing, you will likely need a cleanroom to meet the required cleanliness standards and comply with industry regulations.
- If your industry does not face such strict contamination control requirements, a grey room may be sufficient, offering a more cost-effective solution for your operational needs.
Wiselink Group specializes in designing and installing custom cleanroom solutions that meet the highest industry standards. Our expertise ensures that businesses receive tailored cleanroom environments that meet both regulatory requirements and operational needs.
In summary, the cleanroom vs grey room debate comes down to the level of contamination control, cost, and compliance requirements specific to your industry. Cleanrooms provide the highest levels of cleanliness and air filtration, making them essential for industries like pharmaceuticals, semiconductors, and biotech. On the other hand, grey rooms offer a more relaxed approach to contamination control, making them suitable for industries with lower contamination risks.
By understanding the key differences between these two environments, businesses can make more informed decisions about their environmental needs. Wiselink Group offers expert consultation and custom cleanroom designs that cater to a wide range of industries, ensuring that your environment meets the highest standards of cleanliness, efficiency, and compliance.