Understanding Cleanroom Classifications and Their Importance
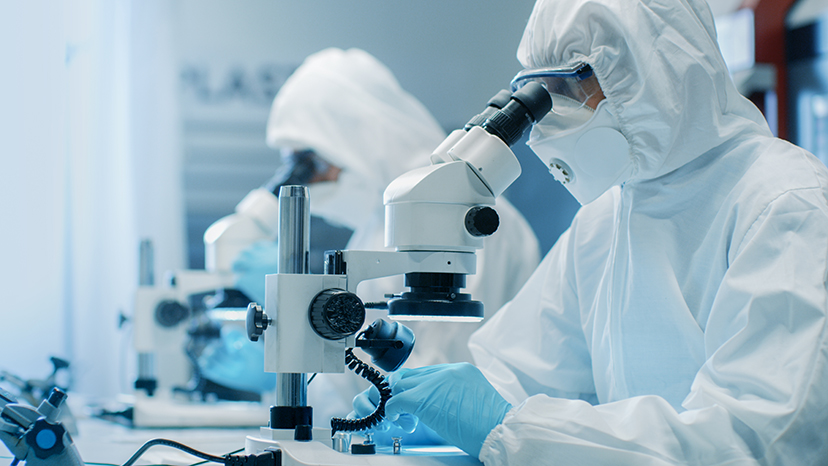
Cleanrooms play an integral role in maintaining controlled environments that ensure the highest levels of product quality, safety, and regulatory compliance. Industries such as pharmaceuticals, biotechnology, semiconductor manufacturing, aerospace, and electronics rely heavily on cleanrooms to achieve the necessary levels of air cleanliness, reduce contamination, and ensure the integrity of their processes.
To understand cleanrooms fully, it’s essential to grasp the concept of cleanroom classifications and the cleanroom standards that define their functionality and operation. Wiselink Group has built a reputation for excellence in designing, installing, and maintaining cleanrooms that meet ISO 14644 classification and ensure the highest standards of cleanliness and safety.
In this blog, we will explore the importance of cleanroom classifications, the ISO 14644 standards, and how different air cleanliness classes dictate the design and functionality of cleanrooms across various industries. We will also delve into the specific cleanroom requirements that businesses must consider to meet compliance, maintain operational efficiency, and safeguard the health and safety of their workers and products.
What is Cleanroom Classification?
Cleanroom classification is a system used to categorize cleanrooms based on the level of airborne particulate contamination present within a given environment. The goal of cleanroom classification is to ensure that the air quality, temperature, and humidity are kept within precise parameters to avoid contamination that could negatively affect sensitive products or processes.
A cleanroom is classified according to the concentration of airborne particles (such as dust, microbes, and other contaminants) per unit of air volume. These concentrations are specified within certain particle sizes, usually in microns, and the cleanroom is designated by a class number. The ISO 14644 standard provides the framework for these classifications, which are vital for ensuring that cleanrooms meet the stringent cleanliness standards required by industries such as pharmaceuticals, medical devices, and semiconductor manufacturing.
Why is Cleanroom Classification Important?
Cleanroom classification is crucial for several reasons, all of which contribute to maintaining the safety, quality, and integrity of the products or processes inside the cleanroom. Here’s why proper classification is essential:
- Product Quality and Integrity: Ensures that no contamination interferes with manufacturing processes, keeping products free from particulate matter or microbial contamination.
- Regulatory Compliance: Adherence to standards like ISO 14644 ensures that businesses meet regulatory requirements, reducing the risk of fines, sanctions, or legal challenges.
- Worker Safety: Proper classification helps create a safe working environment by controlling exposure to harmful particles, chemicals, or other airborne hazards.
- Process Efficiency: Classifications help determine the necessary equipment and operational procedures required to maintain cleanliness, improving process efficiency and consistency.
At Wiselink Group, cleanroom classification is central to every design and installation project. Our team ensures that each cleanroom meets the specific standards required by the client’s industry, providing customized solutions that optimize cleanroom performance.
The ISO 14644 Classification Standard: A Comprehensive Overview
The ISO 14644 standard is the international benchmark for classifying cleanrooms and controlled environments. This standard is divided into several parts, with ISO 14644-1 being the most important as it defines the classification of air cleanliness based on particulate concentration. The classification system within ISO 14644-1 categorizes cleanrooms from Class 1 to Class 9, with Class 1 being the cleanest.
ISO 14644-1 Cleanroom Classification
The ISO classification system categorizes cleanrooms into different classes based on the permissible number of particles of specific sizes per cubic meter of air. These classes are defined by the size of the particles, ranging from 0.1 microns to 5 microns, and are grouped as follows:
- Class 1: The highest level of cleanliness, allowing only 1 particle per cubic meter of air for particles of 0.1 microns in size. This class is used for the most critical processes, such as semiconductor manufacturing and nanotechnology.
- Class 2: Allows up to 10 particles per cubic meter for 0.1-micron particles. Typically used for pharmaceutical manufacturing and medical device assembly.
- Class 3 to 5: These classes are commonly used in pharmaceutical and biotech industries where the cleanliness requirements are slightly less stringent but still crucial for ensuring product quality.
- Class 6 to 9: These classes are used for less stringent cleanroom applications, where higher levels of contamination can be tolerated. Industries such as electronics and automotive manufacturing may require these classes.
It’s important to note that the classification is not just based on particle count. The air cleanliness class also considers the size of particles present, which dictates the level of air filtration and ventilation required for each cleanroom.
How Wiselink Group Implements ISO 14644-1
At Wiselink Group, we specialize in cleanroom design and installation that meets the strictest ISO 14644 classification standards. Our team collaborates with clients to determine the ideal cleanroom classification for their specific needs. Whether you require a Class 1 cleanroom for semiconductor production or a Class 7 cleanroom for general manufacturing, we tailor each solution to meet your industry’s requirements.
We not only ensure that your cleanroom meets the appropriate ISO standards, but we also help with ongoing validation and certification to maintain compliance over time.
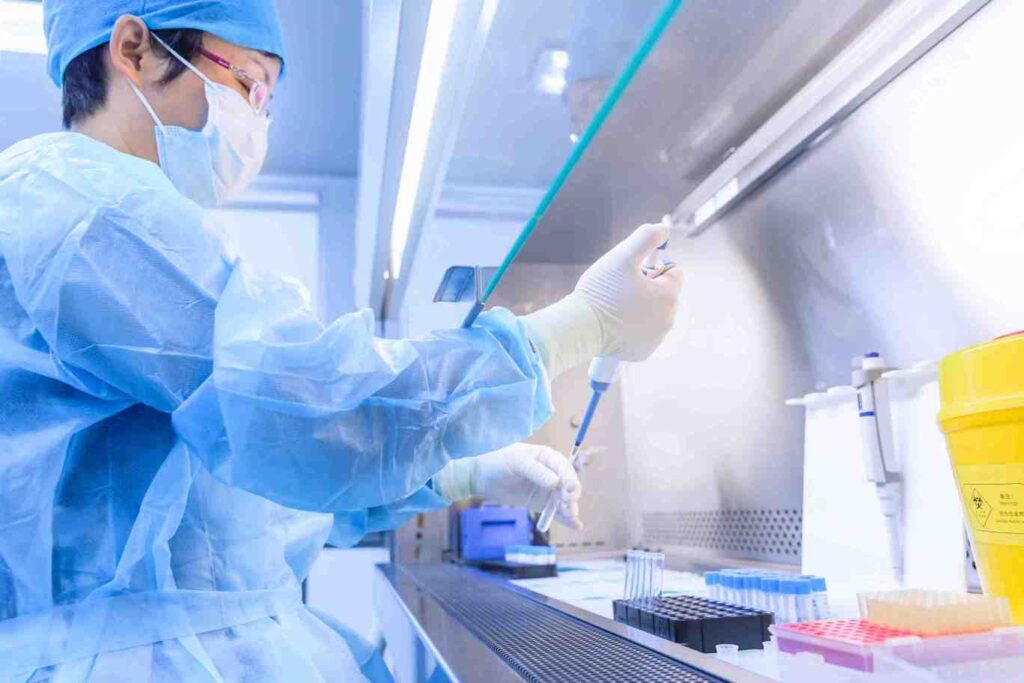
Air Cleanliness Classes: Understanding the Specific Requirements
Air cleanliness classes represent the most critical factor in cleanroom classification. They determine the permissible number of particles per cubic meter of air and influence the design and operational standards of the cleanroom. Below is a deeper look at the different air cleanliness classes and their corresponding particle size and allowable limits:
- Class 1: Permits a maximum of one particle per cubic meter for 0.1-micron particles, and this class is used for the most sensitive processes that demand ultra-clean environments. These environments typically require advanced filtration and ultra-low penetration air (ULPA) filters.
- Class 5: Allows a maximum of 3,520 particles of 0.5 microns per cubic meter. Class 5 cleanrooms are commonly used in pharmaceutical production and other industries requiring stringent standards for air quality.
- Class 7: Allows up to 352,000 particles per cubic meter of air at 0.5 microns. This class is often employed in less critical applications, such as electronics assembly or general industrial processes.
- Class 8: Typically used for commercial and industrial environments where contamination is not as critical but still must be managed effectively. It allows up to 3,520,000 particles per cubic meter.
Key Factors Affecting Air Cleanliness Classes
Several factors influence the air cleanliness class of a cleanroom, including:
- Filtration Systems: The effectiveness of the cleanroom’s air filtration system plays a pivotal role in determining the air cleanliness class. HEPA and ULPA filters are commonly used in higher-class cleanrooms to capture smaller particles.
- Airflow and Ventilation: Wiselink Group designs cleanrooms with carefully controlled ventilation systems that maintain consistent airflow and prevent contamination. Higher cleanliness classes require a more intricate design to ensure that air flows smoothly, without creating turbulence or dead zones.
- Room Design and Materials: The design and construction materials used in cleanroom construction also affect the cleanroom’s ability to maintain air quality. Smooth, non-porous surfaces are used to minimize contamination sources, while airlocks and gowning areas prevent contaminants from entering the cleanroom.
Cleanroom Requirements and Compliance
To ensure that cleanrooms meet specific operational standards, companies must adhere to rigorous cleanroom requirements set by industry regulations. These standards help organizations ensure that their cleanrooms are not only meeting the necessary cleanliness levels but also maintaining regulatory compliance.
Key Cleanroom Requirements
Some of the most important cleanroom requirements that businesses must meet include:
- Temperature and Humidity Control: Maintaining a specific range of temperature and humidity levels is critical to achieving cleanroom compliance. Too much moisture or heat can lead to contamination or negatively affect the manufacturing process.
- Particle and Microbial Control: Cleanrooms must have appropriate filtration systems in place to capture particles, bacteria, and other contaminants. Regular testing and validation help maintain particle control.
- Pressure Differentials: Cleanrooms are often designed with pressure differentials to prevent the entry of contaminated air from outside the cleanroom. These differentials must be monitored and controlled to maintain a consistent and clean environment.
- Personnel and Process Control: Strict protocols for personnel behavior, such as gowning procedures, as well as process control measures, help limit contamination risks in cleanrooms. Worker training and adherence to these protocols are vital for maintaining cleanroom integrity.
Wiselink Group helps businesses adhere to these cleanroom requirements by providing expert guidance and implementing state-of-the-art designs and equipment that maintain regulatory standards.
The Importance of Cleanroom Classifications
In conclusion, understanding cleanroom classifications and their importance is vital for businesses that require controlled environments for sensitive processes. By adhering to ISO 14644 classification and understanding the specific air cleanliness classes, businesses can ensure that their cleanrooms meet industry standards, provide the highest level of protection against contamination, and maintain compliance with regulatory requirements.
Wiselink Group is committed to providing businesses with expert cleanroom design, installation, and maintenance solutions that meet the most stringent cleanroom standards. Whether you require pharmaceutical cleanrooms, semiconductor cleanrooms, or specialized environments for other industries, Wiselink Group ensures that your cleanroom meets the highest classification requirements to ensure safety, compliance, and operational efficiency.