Your Trusted Partner for Cleanroom Solutions & Modular Construction
Custom-Designed, High-Quality Cleanroom Panels, Equipment, and Building Solutions Delivered with Precision.
For over 15 years, Wise Link has been providing innovative cleanroom engineering solutions tailored to your industry’s exact needs. From cleanroom panels to industrial building systems, we ensure your facility is built to the highest standards of cleanliness, efficiency, and quality. Trust us to deliver fast, reliable, and customized solutions for your next project.
Perform At Your Peak
Our Cleanroom Solutions in Action
Comprehensive Solutions for Cleanrooms and Industrial Buildings
We specialize in designing and manufacturing a wide range of products for cleanroom environments and modular construction, ensuring compliance with GMP, WHO, and ISO standards. Our products are engineered for durability, easy installation, and maximum efficiency, providing solutions that fit your project needs.
Recently Added
-
ZP1100 Rotary Tablet Press
Read more -
ZP1100A Rotary Tablet Press
Read more -
GZPK370 Series High Speed Rotary Tablet Press
Read more -
GZP(K) Series High-Speed Rotary Tablet Press
Read more -
GZP(K)730 Series High-Speed Rotary Tablet Press
Read more -
GZP(K)620 Series High-Speed Rotary Tablet Press
Read more -
GZP 570 Series High Speed Rotary Tablet Press
Read more -
GZP(K)520 Series High Speed Rotary Tablet Press
Read more -
Dx51d Z150 Galvanized Steel Coil
Read more -
Matt PPGI Coil – Textured Prepainted Galvanized Steel Coil
Read more -
Flower Painted PPGI (Prepainted Galvanized Steel Coil)
Read more -
Woodgrain PPGI PPGL
Read more -
Brick Pattern PPGI
Read more -
Galvanized Steel Coil and Strip
Read more -
Galvalume Steel Coil
Read more -
Prepainted Aluminum Coil
Read more
Tailored Solutions for Every Industry
Wise Link serves a broad range of industries that demand the highest standards of cleanliness and structural integrity. From pharmaceuticals to food processing, our cleanroom and modular building solutions are designed to meet the specific needs of your industry.
A Step-by-Step Process Designed for Success
From the initial inquiry to the final delivery, we ensure a smooth and efficient process that meets your project’s specific needs. Our team provides full support at every step, from design consultation to prototyping and quality control.
- Consultation & Quote: Provide your project details, and we’ll recommend the best-suited solution.
- Prototyping & Approval: We create prototypes for your inspection before starting production.
Experience, Innovation, and Reliability
At Wise Link, we pride ourselves on being more than just a supplier. We are your strategic partner, providing custom-designed products and services that enhance the performance and efficiency of your facility. With a focus on innovation, quality control, and customer satisfaction, we are committed to helping you succeed.
Main Products
-
50mm PPGI Rockwool Sandwich Wall Panel Modular Cleanroom for Food Workshop with CE
Read more -
Steel Structure used Glass Wool Sandwich Panel For outside cladding system
Read more -
Prefabricated Metal Construction Building Materials EPS Sandwich Wall Panel for Sale
Read more -
Steel Building Glass Wool Sandwich Wall Panel
Read more -
Clean Room Pass Box Without Interlock
Read more -
Cold Room Panel
Read more -
Clean Room Sandwich Panels
Read more -
Cleanroom Window
Read more -
Metal Steel Cleanroom Doors for Hospital
Read more
Explore Our High-Quality Cleanroom Products
Prefabricated Cleanroom Panels
Durable, easy-to-install panels designed for various cleanroom setups. View Details →Stainless Steel Furniture
Non-contaminating, corrosion-resistant furniture to support cleanroom operations. View Details →Industrial Cleanroom Doors
Airtight, easy-to-clean doors that maintain environmental control. View Details →Air Showers & Pass Boxes
Effective solutions for personnel and material transfer. View Details →
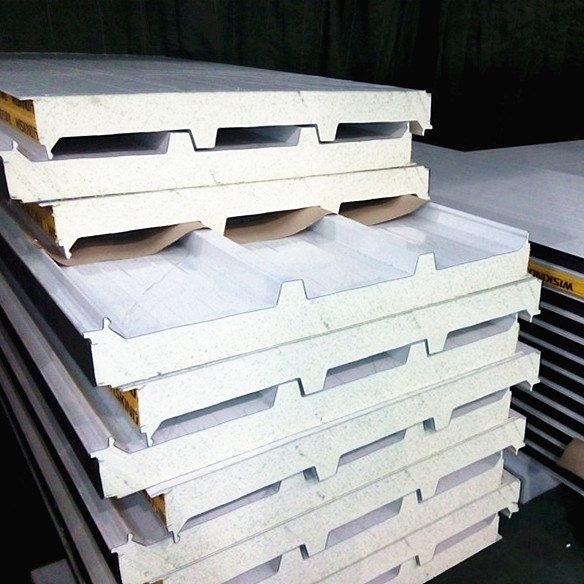
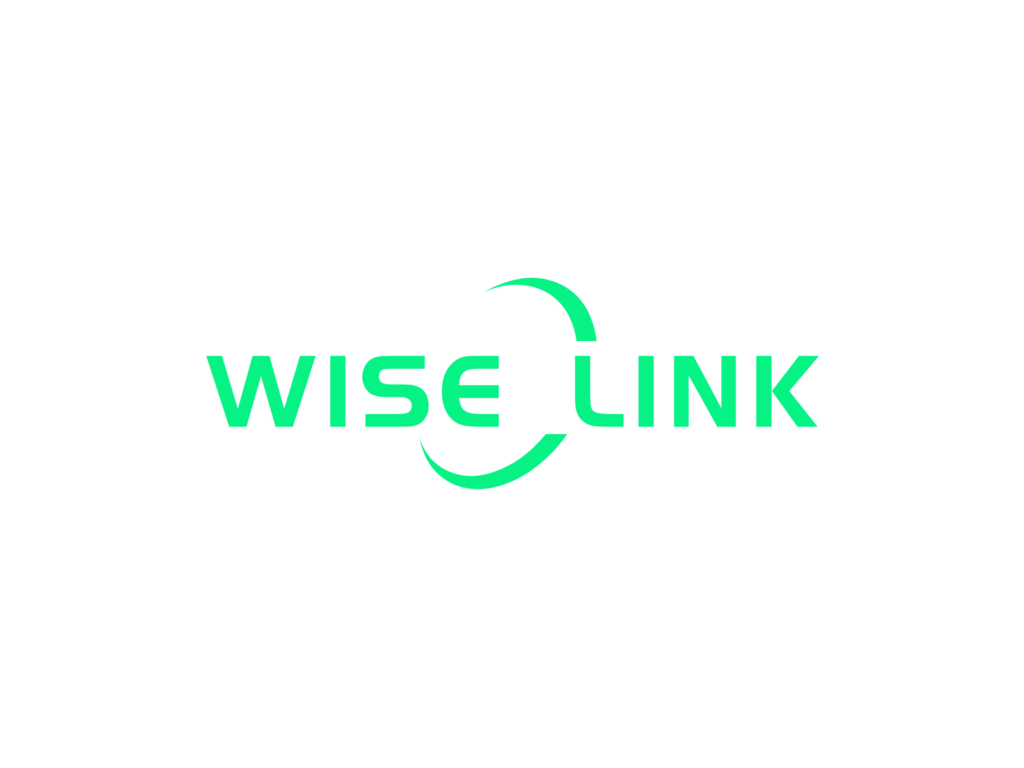
Why Wise Link?
Wise Link delivers top-quality, GMP and ISO-compliant cleanroom solutions with a focus on innovation, efficiency, and customized designs. Our expert team ensures seamless support from design to maintenance, tailored to your industry’s unique needs.
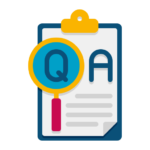
Quality Assurance
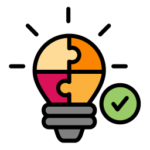
Custom Solutions
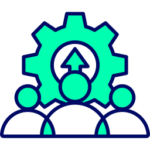
Expert Engineering Team
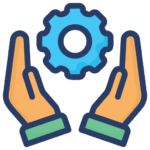
Comprehensive Support
FAQs
What industries does Wise Link serve with cleanroom solutions?
We provide cleanroom solutions for a variety of industries, including pharmaceuticals, biotechnology, electronics, aerospace, and healthcare. Our designs are tailored to meet the specific requirements and regulatory standards of each sector.
Are your cleanroom systems compliant with GMP and ISO standards?
Yes, all our cleanroom systems are designed to be fully compliant with GMP (Good Manufacturing Practice) and ISO standards, ensuring high levels of cleanliness, safety, and efficiency for sensitive production environments.
Can you customize cleanroom designs based on specific needs?
Absolutely. We specialize in custom cleanroom designs that cater to the unique requirements of each client, whether you need a modular setup, specialized filtration, or custom environmental controls.
What is the typical installation time for a cleanroom?
The installation time varies depending on the size and complexity of the cleanroom, but our modular construction solutions allow for faster setup compared to traditional methods, minimizing downtime.
Do you offer ongoing maintenance and support for cleanrooms?
Yes, we provide comprehensive support services, including routine maintenance, system upgrades, and repairs to ensure your cleanroom operates efficiently and remains compliant over time.
How can I get a quote for my cleanroom project?
You can easily request a quote by contacting us through our website, email, or phone. Our team will discuss your project requirements and provide a detailed, custom quote to meet your needs.
What are the benefits of modular cleanroom construction?
Modular cleanrooms offer flexibility, faster installation, and scalability, making them an ideal solution for facilities that may need to expand or reconfigure their cleanroom spaces in the future.
What environmental controls can Wise Link integrate into cleanroom systems?
We can integrate advanced HVAC systems, HEPA/ULPA filtration, temperature and humidity controls, and real-time monitoring systems to maintain optimal environmental conditions in your cleanroom.
Do you provide cleanroom products like pass boxes, air showers, and cleanroom panels?
Yes, we offer a wide range of cleanroom products, including prefabricated panels, pass boxes, air showers, and stainless steel furniture, all designed to maintain high cleanliness levels.
How can I ensure my cleanroom remains compliant with industry regulations?
Our team will help you design and maintain your cleanroom according to the latest industry standards. We also offer ongoing monitoring and maintenance services to ensure continuous compliance and optimal performance.
Empower Your Industry with Comprehensive Cleanroom Solutions
From custom design and modular construction to advanced engineering and compliance, our solutions drive precision, efficiency, and excellence across pharmaceuticals, biotechnology, electronics, and more. Get in touch today to transform your cleanroom operations!